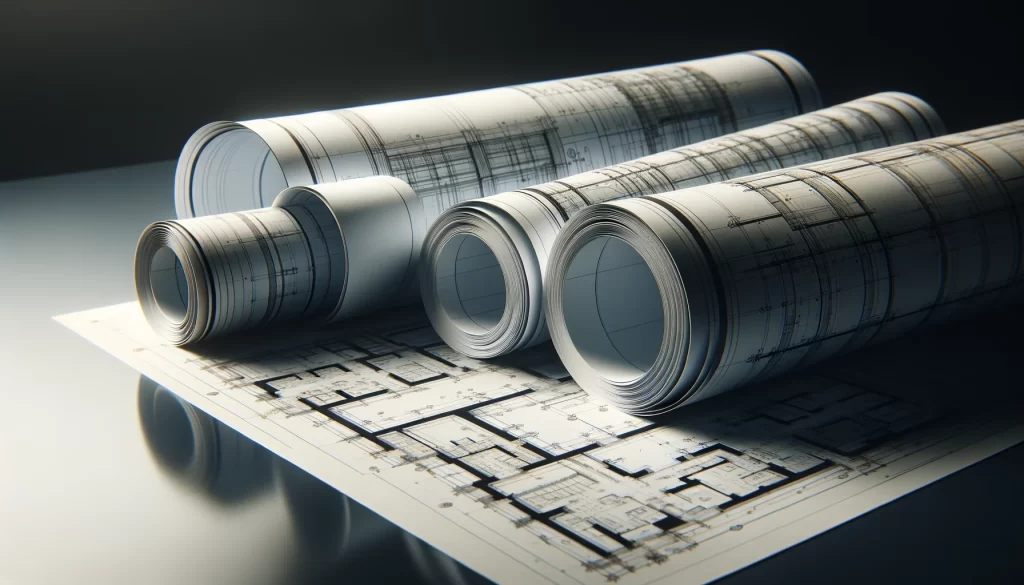
TELEMATICS
Blueprints
This blueprint offers a practical, step-by-step guide to telematics implementation for fleet optimization, covering deployment, integration, and performance management.
Rising fuel costs, incident liability, and labor variability continue to expose performance gaps in fleet operations, despite increased digitization elsewhere in the supply chain. For many organizations, the absence of real-time visibility into vehicle health, driver behavior, and route compliance has become a structural constraint on safety, efficiency, and cost control.
In response, supply chain leaders are implementing advanced telematics as a core operational capability. Companies including PepsiCo and DB Schenker are integrating telematics data into dispatch, maintenance, and risk management processes to improve decision-making at speed and scale.
This blueprint provides a practical, step-by-step guide to telematics implementation for fleet optimization. It addresses architecture design, vendor selection, cross-functional integration, behavioral change management, and performance monitoring, enabling organizations to move from fragmented pilots to sustained operational impact.
Implementation Steps: A Comprehensive Guide to Telematics Deployment for Fleet Optimization
This step-by-step guide provides supply chain leaders with a structured and granular approach to implementing advanced telematics across medium to large fleet operations. The process reflects enterprise-level complexity, change management requirements, and integration needs—ensuring that safety, fuel efficiency, and operational insight are materially improved.
Step 1: Define Strategic Objectives and Governance Structure
- 1.1 Link Telematics to Enterprise KPIs
– Align telematics objectives with strategic goals: reduce cost per mile, lower fuel consumption, minimize safety incidents, and support Scope 1 emissions tracking.
– Validate objectives with CFO, COO, and sustainability leads to secure enterprise-wide commitment. - 1.2 Establish a Fleet Telematics Governance Council
– Form a cross-functional steering group including fleet ops, IT, risk/compliance, finance, HR, and legal.
– Define authority for decisions on vendor selection, data use policy, and change management strategies. - 1.3 Conduct Current State Maturity Assessment
– Audit current fleet visibility and digital maturity across hardware, software, and analytics capabilities.
– Use a structured model like Gartner’s Fleet Technology Maturity Framework to benchmark readiness across five key domains.
Step 2: Build the Business Case and Value Model
- 2.1 Quantify the Cost of Inaction
– Analyze historical data on fuel usage, maintenance spend, incident rates, and route efficiency.
– Identify and assign hard costs to inefficiencies such as idle time and harsh driving patterns. - 2.2 Model Financial Benefits and Strategic Upside
– Create a detailed TCO and ROI projection, incorporating operational savings and regulatory impact avoidance.
– Include scenario planning for different fuel price and regulation environments. - 2.3 Define Success Metrics for Post-Implementation Review
– Establish clear success targets (e.g., % improvement in MPG, reduction in downtime).
– Create a cadence for quarterly KPI reviews with finance, operations, and fleet leadership.
Step 3: Select Technology Architecture and Vendors
- 3.1 Define Architecture Requirements Across Layers
– Specify needs across device, connectivity, software platform, and cybersecurity layers.
– Confirm CAN bus compatibility, cellular coverage, and cloud platform integration. - 3.2 Apply a Scoring Model for Vendor Shortlisting
– Use a weighted criteria matrix: functionality, data integration, global coverage, SLA terms, pricing model.
– Score vendors based on alignment with long-term fleet strategy and compliance mandates. - 3.3 Conduct Pilot Testing with Top Vendors
– Run trials across representative routes and vehicle types.
– Collect feedback from drivers, supervisors, and dispatchers to assess user fit and reliability.
Step 4: Design and Execute Integration Roadmap
- 4.1 Create a Systems Integration Blueprint
– Map telematics data flow into core systems (ERP, TMS, fleet maintenance platforms).
– Define API integration, middleware protocols, and reporting layers. - 4.2 Establish Real-Time Operational Workflows
– Build live dashboards and rules-based alerts for geofencing, diagnostics, and route compliance.
– Link automated alerts to maintenance scheduling and dispatch workflows. - 4.3 Coordinate Data Privacy and Regulatory Compliance
– Ensure data governance complies with GDPR, CCPA, and local transport safety regulations.
– Define policies on driver data use, anonymization, and retention schedules.
Step 5: Manage Organizational Change and Driver Adoption
- 5.1 Launch Targeted Change Management Program
– Use a formal framework (e.g., ADKAR or Kotter) to manage resistance and sustain engagement.
– Develop messaging that aligns with safety culture and performance incentives. - 5.2 Implement Tiered Training Plans
– Deliver role-specific training for drivers, dispatchers, IT, and management.
– Include scenario-based simulations and real-world data interpretation sessions. - 5.3 Design Performance and Incentive Structures
– Link telematics KPIs (e.g., idle time, braking score) to recognition programs and financial incentives.
– Use gamified leaderboards and peer comparisons to foster healthy competition.
Step 6: Operationalize Performance Monitoring and Optimization
- 6.1 Build Cross-Functional Telematics Dashboarding
– Create role-based dashboard views with tailored metrics and alerts.
– Include automated reports for exception handling and trend analysis. - 6.2 Apply Predictive and Prescriptive Analytics
– Deploy ML models for route optimization, fuel efficiency forecasting, and maintenance risk prediction.
– Use insights to guide SOP updates and capacity planning. - 6.3 Conduct Post-Implementation Reviews and Iteration Cycles
– Evaluate adoption rates, business impact, and system reliability quarterly.
– Adjust policy, tech configuration, and engagement plans based on real-world performance data.
Step 7: Scale and Future-Proof the Telematics Program
- 7.1 Create a Global Expansion Roadmap
– Analyze region-specific regulatory requirements and network coverage constraints.
– Develop expansion kits for standardized training, policy, and infrastructure rollout. - 7.2 Integrate with Broader Digital Fleet Strategy
– Connect telematics to digital twins, supply chain control towers, and cold chain systems.
– Explore integration with EV fleet management, battery diagnostics, and smart charging systems. - 7.3 Benchmark and Participate in Industry Collaboration
– Engage in external benchmarking, data collaboratives, and insurer-backed performance reviews.
– Use audit results to drive continuous improvement and strategic differentiation.
Key Metrics and KPIs for Telematics-Driven Fleet Optimization
Tracking the right KPIs is essential to evaluate the operational and financial return of a telematics implementation for fleet optimization. These metrics should be monitored regularly through centralized dashboards and reviewed in operational planning cycles.
1. Fuel Efficiency (MPG or Liters/100km)
Monitor changes in average fuel consumption across vehicles and routes. Segment by driver and route profile to isolate improvement areas. Pair this with idling data to identify avoidable fuel burn.
2. Driver Behavior Score
Track safety-related behaviors such as speeding, harsh braking, acceleration, and cornering. Many platforms assign composite safety scores—use these to drive coaching conversations and reward top performers.
3. Idle Time per Vehicle/Route
Measure total and per-trip idle time. Set thresholds based on vehicle class and usage patterns. Excessive idling often signals routing inefficiencies or poor driver discipline.
4. Maintenance Predictive Accuracy
Use telematics-triggered diagnostics to predict and schedule vehicle servicing. Track the ratio of unplanned vs. planned maintenance and correlate to uptime targets.
5. Safety Incident Rate (per 100,000 miles/km)
Integrate incident data (collisions, near-misses) with telematics logs. Look for correlations with behavior scores and use findings to refine training and route risk models.
These KPIs should be reviewed in weekly operational dashboards and monthly performance reviews. Over time, patterns in these indicators will help quantify ROI and guide further optimization of your fleet strategy.
Best Practices for Embedding Telematics in Supply Chain Operations
Successful telematics implementation for fleet optimization requires more than just system deployment—it demands operational alignment, policy discipline, and sustained stakeholder engagement. The following best practices support long-term value realization and minimize disruption during rollout and scale-up.
1. Treat Telematics as a Change Program, Not a Tech Project
Adoption hinges on cross-functional engagement, especially from fleet operations, compliance, and HR. Formalize program sponsorship at the executive level, and assign a dedicated change lead to manage training, feedback loops, and internal communications.
2. Standardize Data Definitions and Ownership
Inconsistent interpretation of metrics—such as what qualifies as “harsh braking” or “idle time”—can create internal conflict and undermine credibility. Define and document operational thresholds, ownership roles, and escalation protocols to ensure consistent usage across locations and teams.
3. Balance Compliance With Trust in Driver Programs
Driver buy-in is critical. Avoid over-surveillance and instead position telematics as a support mechanism. Use anonymized reporting where appropriate and emphasize coaching over punishment. Establish driver advisory groups to shape rollout policies and monitor sentiment.
4. Establish Clear Data Review Cadences
Set weekly and monthly intervals for reviewing key metrics with operational leads—such as fuel consumption per route, safety incidents by region, and maintenance alerts. Use consistent formats and data visualization to build institutional familiarity and actionable insight.
5. Build Internal Capability Early
Avoid over-reliance on third-party vendors post-implementation. Develop internal skills in fleet analytics, dashboard configuration, and exception reporting to ensure the organization can scale and adapt its telematics systems without vendor bottlenecks.
Used alongside the implementation roadmap, these best practices will help ensure your telematics program delivers sustained safety, efficiency, and cost reduction benefits across your fleet operations.
Implementation Challenges and How to Overcome Them
While the benefits of telematics implementation for fleet optimization are well-documented, operationalizing these systems in large-scale supply chains is rarely frictionless. Below are five common challenges supply chain leaders face during deployment, along with practical solutions to mitigate them.
1. Data Overload and Low Actionability
Many organizations find themselves overwhelmed by telematics data streams without the ability to interpret or act on them effectively. This can lead to analysis paralysis or missed insights.
Solution: Define a core set of operational KPIs in advance (e.g., fuel per mile, idle time, maintenance triggers), and configure dashboards to filter noise. Assign data stewardship roles to operations analysts who can translate signals into workflows and decisions.
2. Integration with Legacy Systems
Legacy TMS or ERP systems may not readily support API-based integration with telematics platforms, creating data silos and manual workarounds.
Solution: During vendor selection, prioritize platforms with middleware or integration toolkits that support modular deployments. Engage IT early to define data architecture and avoid latency or duplication issues.
3. Driver Resistance and Trust Issues
Drivers may view telematics as a surveillance tool rather than a safety or performance enabler, leading to disengagement or deliberate circumvention.
Solution: Involve driver representatives in policy development and communication planning. Emphasize coaching over penalties, and use anonymized reporting during early phases to build credibility.
4. Lack of Cross-Functional Ownership
Telematics often sits between departments—IT, fleet, compliance, sustainability—leading to unclear accountability and misaligned incentives.
Solution: Establish a formal governance structure with shared KPIs and escalation paths. Create a steering committee with decision rights and budget oversight across functions.
5. Underestimation of Total Cost and Time to Value
Organizations often underestimate the complexity of hardware installation, training, and post-launch optimization. This can delay ROI or cause scope creep.
Solution: Conduct phased pilots with detailed cost tracking. Include change management, training, and integration labor in the TCO model. Set realistic time horizons for stabilization—typically 6 to 12 months for mid-sized fleets.
By anticipating these challenges early in the telematics implementation for fleet optimization journey, supply chain leaders can avoid delays, control risk, and accelerate performance gains.
This blueprint provides supply chain teams with a structured, execution-focused approach to telematics implementation for fleet optimization. By following the steps outlined, organizations can enhance driver safety, reduce fuel and maintenance costs, and unlock real-time operational visibility without displacing existing systems. For additional guidance on integration architecture, behavior change strategies, or scaling across multiple geographies, refer to – FAQs: Embedding Telematics for Fleet Visibility and Optimization.
To access more execution-ready blueprints and strategic resources tailored for logistics, operations, procurement, and supply chain leaders, subscribe to SupplyChain360. Join now and transform your supply chain management approach!