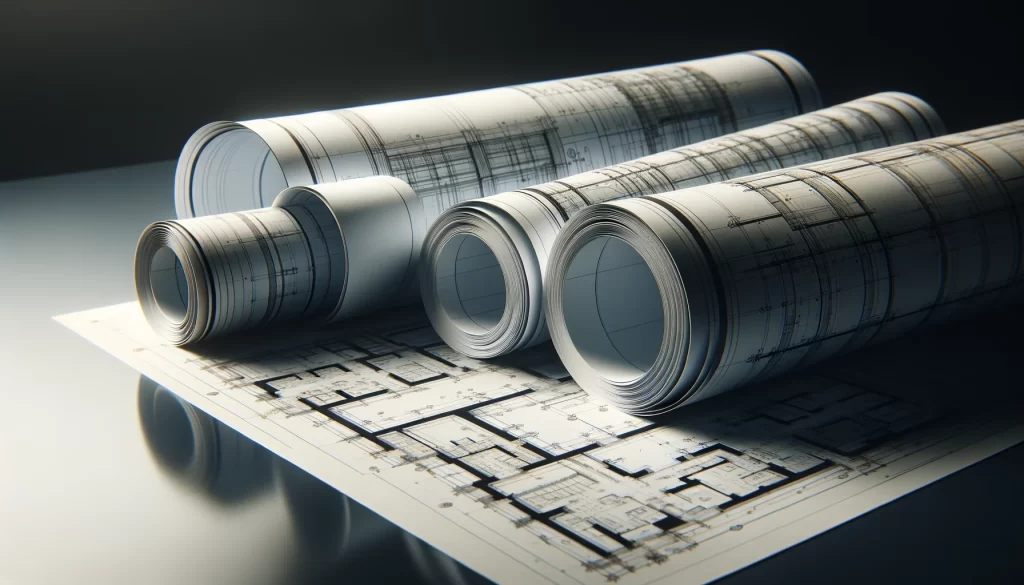
Supply Chain Collaboration and Integration
Blueprints
Supplychain360 blueprints offer an extensive collection of toolkits enabling swift access to best practice to enhance operations or to enable robust decision making.
Implementing advanced fleet telematics is crucial for multinational supply chain operations aiming to optimize efficiencies and reduce costs. This blueprint offers a systematic approach to integrating cutting-edge telematics, addressing high fuel consumption and prolonged delivery times directly.
By following the structured steps, best practices, and KPIs outlined, supply chain leaders can achieve measurable improvements in fleet performance. This document provides actionable insights and clear guidelines for navigating telematics technology, facilitating smoother transitions, better route management, reduced operational costs, and improved service delivery across global supply chains.
Step-by-Step Guide to Implementing Advanced Fleet Telematics
Step 1: Assessment of Current Fleet Management Systems
– Objective Evaluation: Conduct detailed audits including vehicle diagnostics, route logging, and driver behavior analysis. Use advanced analytics to assess the efficiency of current routing versus industry benchmarks. Identify specific inefficiencies like excessive idling, route deviations, and underutilization of assets.
– Needs Analysis: Facilitate workshops with key stakeholders to understand their pain points and expectations from a telematics solution. Analyze scalability requirements for expanding operations or fleet size changes.
– Framework Utilization: Employ the SWOT analysis to evaluate internal capabilities and external opportunities for leveraging telematics technology. Use the GAP analysis to detail the current versus required capabilities for optimized fleet management.
Step 2: Technology Selection
– Setting Criteria for Selection: Establish criteria such as data update frequency, system reliability under varying conditions, and ease of integration with existing systems. Consider additional features like predictive maintenance alerts, driver safety monitoring, and automated reporting capabilities.
– Vendor Evaluation and Selection: Conduct comprehensive RFP (Request for Proposal) process, inviting leading vendors to submit their proposals. Organize vendor demonstrations tailored to your specific operational scenarios to evaluate system performance firsthand.
– Compliance and Security: Review all telematics solutions for compliance with the latest international regulations such as ePrivacy Directive and local laws. Ensure robust encryption practices for data transmission and storage to safeguard sensitive information.
Step 3: System Integration
– Integration Planning: Map out the IT architecture integration with telematics to support data flow and storage. Plan for minimal disruption during integration, potentially scheduling during low activity periods.
– Execution of Integration: Implement APIs or middleware for seamless data integration between telematics software and existing fleet management or ERP systems. Perform extensive testing phases to validate the integration, including stress tests and performance benchmarking.
– Risk Management: Develop contingency plans for data breaches, system downtimes, and other IT risks. Establish regular system audits post-integration to ensure ongoing performance and security standards are met.
Step 4: Staff Training and Support
– Training Program Development: Develop comprehensive training curricula that include user manuals, quick-reference guides, and scenario-based learning. Include advanced modules on data analytics for managers to effectively utilize telematics data for strategic decision-making.
– Training Delivery: Implement blended learning approaches, combining in-person sessions with virtual simulations and webinars. Schedule periodic refresher courses and update training content as new features or updates are released.
– Support Structures: Set up a tiered support system to provide personalized support across different user levels and regions. Implement user satisfaction surveys to identify areas for improvement in training and system usability.
Step 5: Deployment and Go-Live
– Pilot Testing: Design pilot tests to measure specific performance indicators against predefined targets. Use control groups and varying scenarios to comprehensively understand system impacts under different conditions.
– Full-Scale Rollout: Develop a rollout schedule that prioritizes critical fleet segments or regions that could benefit most from early deployment. Use change management principles to manage the transition, addressing resistance and fostering positive attitudes towards the new system.
– Post-Deployment Review: Utilize advanced data analytics to measure the impact of telematics on operational efficiency and cost savings. Establish a continuous improvement team to take charge of ongoing enhancements and leverage learnings for other parts of the business.
Best Practices for Effective Implementation of Advanced Fleet Telematics in Supply Chain Operations
Align Telematics Goals with Business Objectives: Clearly define how the telematics system will support broader business goals such as reducing costs, improving delivery times, or enhancing customer satisfaction. This alignment ensures that the implementation is driven by strategic objectives, enhancing its relevance and value.
Engage Stakeholders Early: Involvement of all key stakeholders from the initial stages is crucial. This includes not only the logistics team but also drivers, IT staff, and senior management. Early engagement helps in addressing concerns, gaining buy-in, and leveraging insights from different parts of the organization which can lead to more effective integration and usage of the telematics system.
Ensure Robust Training and Support: Comprehensive training programs are essential for both end-users (e.g., drivers and logistics managers) and IT staff who will maintain the system. Training should cover operational use of the system, data interpretation, and troubleshooting. Ongoing support should be structured to provide quick resolutions to operational hiccups, ensuring minimal disruption to supply chain activities.
Implement Incrementally: Rather than a full-scale rollout, consider a phased approach where the telematics system is implemented in stages. This allows for addressing any issues on a smaller scale and making adjustments before a wider deployment. It also helps in managing change more effectively within the organization.
Leverage Data Analytics: With advanced fleet telematics, vast amounts of data are generated which can provide insightful analytics on fleet performance, route optimization, and driver behavior. Develop capabilities to analyze this data to continually refine and improve supply chain operations.
Focus on Continuous Improvement: Telematics technology evolves rapidly; thus, maintaining an approach of continuous improvement is vital. Regularly review the system’s performance, stay updated with new features and technologies, and be ready to adapt the system as needed to meet changing operational demands.
Ensure Compliance and Security: Always ensure that the telematics system complies with local and international regulations regarding data protection and fleet management. Prioritizing cybersecurity and data privacy not only protects the organization but also builds trust with your clients and partners.
Key Metrics and KPIs to Measure Success in Fleet Telematics Implementation
Fuel Efficiency: Measure the average fuel consumption per mile across the fleet before and after telematics implementation. A decrease in fuel consumption indicates effective route optimization and driver behavior management. Utilize fuel consumption logs and telematics data for accurate tracking.
On-Time Delivery Rates: Track the percentage of deliveries that arrive on schedule. This KPI is crucial for customer satisfaction and operational reliability. Telematics systems provide real-time data on vehicle locations and estimated arrival times, enabling precise tracking of this metric.
Vehicle Utilization: Monitor the daily active usage of each vehicle in the fleet to assess whether the fleet size is optimized for the volume of work. Higher utilization rates without an increase in maintenance costs suggest efficient use of assets.
Idle Times: Measure the amount of time vehicles spend idling. Excessive idling not only wastes fuel but also contributes to vehicle wear and tear. Telematics can help identify and reduce unnecessary idle times through alerts and reporting.
Maintenance Costs: Track the total maintenance expenditure per vehicle and compare it pre- and post-telematics implementation. Effective telematics should lead to predictive maintenance schedules, potentially lowering these costs by preventing major repairs.
Driver Safety Scores: Compile safety scores based on data about hard braking, rapid acceleration, and speeding. Improvements in these scores indicate successful driver behavior modification facilitated by telematics feedback.
These KPIs should be regularly reviewed and analyzed through dashboards that integrate telematics data with other operational data. Effective interpretation of these metrics involves comparing them against set benchmarks and industry standards to ensure that the fleet is not just meeting but exceeding performance expectations. Regularly updating these benchmarks in line with technological advancements and organizational growth is also crucial to maintain relevance and drive continuous improvement.
Overcoming Challenges in Implementing Advanced Fleet Telematics in Supply Chains
Data Integration Complexity: Integrating telematics data with existing IT systems can be complex due to different data formats and legacy systems.
Solution: Employ middleware solutions that can act as a bridge between telematics systems and existing IT infrastructure. Invest in customizable integration platforms that can handle multiple data formats and streamline the flow of information.
Resistance to Change: Employees, especially drivers and operational staff, may resist adopting new technologies, fearing job displacement or increased workload.
Solution: Conduct educational sessions to demonstrate the benefits of telematics, focusing on how it simplifies tasks and improves safety. Implement change management strategies that include staff in the planning and deployment phases to increase buy-in and reduce resistance.
Cost Concerns: The initial investment for advanced telematics systems can be substantial, deterring some companies from implementation.
Solution: Develop a clear ROI analysis that highlights long-term savings from fuel efficiency, reduced downtime, and lower maintenance costs. Consider phased deployments or leasing options to spread out expenses over time.
Privacy and Compliance Issues: Telematics involve tracking driver behavior and vehicle locations, which can raise privacy concerns and compliance issues with data protection laws.
Solution: Ensure telematics systems comply with relevant laws such as GDPR. Be transparent with employees about what data is collected and how it will be used, emphasizing data security measures and the non-intrusive nature of monitoring.
Technical Failures: Hardware malfunctions or software glitches can disrupt telematics operations, leading to data loss or inaccurate data.
Solution: Choose high-quality telematics hardware and software with robust support and warranty agreements. Establish a protocol for regular system checks and maintenance to prevent or quickly resolve technical issues.
Scalability Limitations: As businesses grow, their telematics systems must scale accordingly without losing performance or increasing complexity disproportionately.
Solution: Select telematics solutions that are known for their scalability and can integrate easily with additional modules or updates. Regularly review system capabilities to ensure they meet growing operational needs.
This blueprint equips supply chain leaders with essential strategies for implementing advanced fleet telematics, promising enhanced route efficiency, reduced costs, and improved operational oversight across global supply chains.
Unlock the full potential of your supply chain operations. Subscribe to SupplyChain360 today and gain exclusive access to an extensive collection of blueprints and resources designed to drive efficiency and innovation in your business. Don’t miss out—join the leaders shaping the future of supply chains.