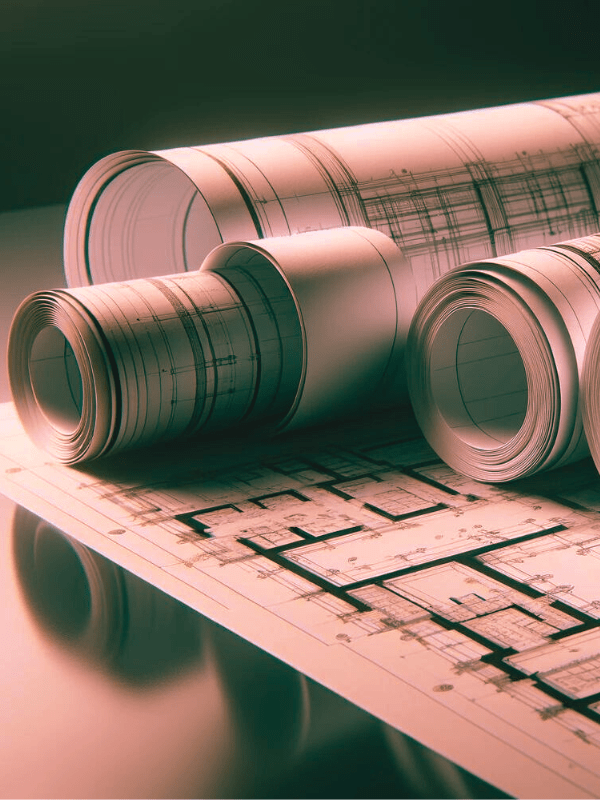
Supply Chain operations series
Collaboration & Compliance
BLUEPRINTS
Managing inventory across multiple channels and partners presents a formidable challenge. The significance of achieving real-time stock visibility in such a complex environment cannot be overstated.
This blueprint provides a structured approach to implementing shared inventory platforms, enhancing transparency and efficiency. By detailing specific steps, tools, and best practices, it directly tackles the obstacles associated with multi-national inventory management.
Utilizing this blueprint empowers companies to optimize supply chain operations, reduce costs, and improve service levels, ensuring a competitive edge in the rapidly evolving market landscape.
Implementation Steps: Establishing an Effective Real-Time Shared Inventory Platform
Step 1: Assessment of Current Inventory Management Systems
- Review Existing Systems: Evaluate current inventory management practices, software, and data handling procedures. Identify gaps in real-time data availability and accuracy.
- Stakeholder Interviews: Conduct discussions with key personnel involved in inventory, procurement, and supply chain management to understand their needs and challenges.
- Benchmarking: Compare current systems against industry standards and best practices to identify areas for improvement.
- Framework for Assessment: Utilize frameworks like SWOT (Strengths, Weaknesses, Opportunities, Threats) analysis to systematically assess capabilities and identify strategic opportunities.
Step 2: Selection of Appropriate Technology Platforms
- Define Requirements: Based on the assessment, list essential features and capabilities needed in the new system, such as real-time tracking, compatibility with existing systems, and scalability.
- Market Research: Research available inventory management systems that cater to large, multi-national companies with complex supply chains.
- Vendor Evaluation Criteria: Establish criteria for selecting vendors, including technology maturity, support services, customization options, and client testimonials.
- Pilot Testing: Choose a shortlist of platforms and conduct pilot tests to evaluate their performance in real-world conditions.
Step 3: Integration Strategies for Real-Time Data Sharing
- Integration Plan: Develop a detailed plan for integrating the new platform with existing ERP systems, e-commerce platforms, and other relevant IT infrastructure.
- API Utilization: Focus on platforms offering robust APIs for seamless data exchange across different systems and partners.
- Data Standardization: Implement data standardization practices to ensure uniformity in data formats, naming conventions, and metrics across all systems and partners.
- Model Adoption: Use the ETL (Extract, Transform, Load) model to manage data effectively between different systems and platforms.
Step 4: Training and Change Management
- Develop Training Materials: Create comprehensive user manuals, training videos, and quick-reference guides tailored to different roles within the organization.
- Training Sessions: Organize hands-on training sessions for all users focusing on day-to-day operations and troubleshooting common issues.
- Change Management Strategy: Employ change management principles from models like ADKAR (Awareness, Desire, Knowledge, Ability, Reinforcement) to manage the human aspects of change during the transition to a new system.
- Feedback Loop: Establish a feedback mechanism to continuously collect user input on system usability and functionality, facilitating ongoing improvements.
Step 5: Continuous Monitoring and Iterative Improvements
- Performance Metrics: Define clear metrics to measure the performance of the new system, such as data accuracy, system uptime, and user satisfaction.
- Regular Audits: Schedule periodic audits of the system to ensure compliance with data standards and to identify any emerging issues or needs.
- Continuous Improvement Plan: Adopt a continuous improvement framework like Six Sigma to systematically refine and enhance system performance over time.
- Scalability Assessments: Regularly review system scalability and adjust resources to meet growing organizational needs or to incorporate additional partners.
Best Practices for Implementing Real-Time Shared Inventory Platforms
To effectively implement a real-time shared inventory platform within supply chain operations, it is essential to adhere to a set of best practices that ensure success, efficiency, and scalability. These guidelines focus on fostering collaboration, ensuring data integrity, and promoting scalability.
- Foster Collaborative Planning and Communication:
- Engage All Stakeholders Early: Include all relevant parties from the onset of the project, from suppliers to logistics partners, to ensure their needs and insights shape the implementation process.
- Regular Communication: Establish a routine for regular updates and feedback sessions across all stakeholders to maintain alignment and address any concerns promptly.
- Ensure Data Integrity and Security:
- Robust Data Governance: Develop a strong governance framework that dictates how data is collected, stored, and accessed. This will help maintain the accuracy and privacy of data.
- Advanced Security Measures: Implement state-of-the-art security protocols and regular audits to safeguard sensitive information and comply with international data protection regulations.
- Emphasize Training and Support:
- Comprehensive Training Programs: Prioritize extensive training for all system users to ensure they are competent in using the new tools and can handle issues that may arise.
- Ongoing Support and Resources: Provide continuous support through a dedicated helpdesk, online resources, and periodic refresher courses to assist users in adapting to system updates or resolving operational challenges.
- Leverage Advanced Analytics and AI:
- Predictive Analytics: Utilize AI-driven tools to analyze data and predict trends, enabling proactive management of inventory levels and optimization of supply chain processes.
- Continuous Analytics: Regularly monitor performance data to identify inefficiencies and areas for improvement, thus continuously refining the supply chain operations.
- Plan for Scalability:
- Scalable Solutions: Choose platforms that offer scalability in terms of adding new partners, handling increased transaction volumes, and expanding into new geographical areas without losing performance.
- Regular System Evaluations: Periodically reassess system capabilities and scalability to ensure it continues to meet evolving business needs and growth.
Implementing these best practices will enhance the functionality and impact of a real-time shared inventory platform, leading to improved transparency, reduced costs, and better overall efficiency in supply chain operations. By integrating these practices alongside the technical steps outlined in the blueprint, companies can maximize the benefits of their investment and achieve a competitive edge in the marketplace.
Tools and Technologies for Real-Time Shared Inventory Platforms
To successfully implement a real-time shared inventory platform in a multinational supply chain, selecting the right tools and technologies is crucial. These tools not only facilitate seamless operations but also enhance the effectiveness of the implementation steps previously outlined.
- Inventory Management Software:
- Features: High-performance inventory tracking, automated reordering, and forecasting capabilities.
- Benefits: Improves accuracy of inventory levels, reduces stock-outs and overstock situations, and optimizes replenishment cycles.
- Integration: Integrates with existing ERP systems to provide a unified view of inventory across all channels, crucial for the assessment and integration strategies in our blueprint.
- Enterprise Resource Planning (ERP) Systems:
- Features: Centralized data management, financial management, and resource planning.
- Benefits: Enhances decision-making through integrated data from various departments, improving operational efficiency and reducing operational costs.
- Integration: ERP systems form the backbone of data standardization and are pivotal in the integration phase, ensuring data consistency across all functions.
- Cloud Platforms:
- Features: Scalable storage, high availability, and broad accessibility.
- Benefits: Enables real-time data sharing across geographical boundaries without significant infrastructure investment.
- Integration: Cloud platforms support API-driven integrations with other systems, crucial for real-time data sharing and standardization in our implementation steps.
- Artificial Intelligence (AI) and Machine Learning (ML):
- Features: Predictive analytics, demand forecasting, and advanced data analytics.
- Benefits: Provides insights into consumer behavior patterns, optimizes inventory levels, and anticipates future trends to mitigate risks.
- Integration: AI tools can be integrated into inventory management software and ERP systems to enhance the predictive capabilities and automate decision-making processes.
- Blockchain Technology:
- Features: Decentralized ledger, immutable records, and enhanced security.
- Benefits: Increases transparency in the supply chain, enhances security of data exchanges, and builds trust among all stakeholders.
- Integration: Blockchain can be integrated to secure data sharing during real-time transactions, supporting data integrity and security in the blueprint’s implementation.
These technologies, when effectively integrated into the supply chain operations as outlined in the blueprint, will significantly enhance the efficiency, transparency, and responsiveness of inventory management practices. This will enable multinational companies to better manage their supply chains in a dynamic global market.
Key Metrics and KPIs for Measuring Success in Shared Inventory Platforms
To effectively monitor and evaluate the performance of real-time shared inventory platforms, supply chain directors should focus on specific Key Performance Indicators (KPIs) that reflect the efficiency and effectiveness of their operations. Here are essential metrics that are crucial for tracking the success of these implementations:
- Inventory Accuracy:
- Definition: Measures the match percentage between recorded inventory and actual physical stock.
- Tracking: Conduct regular cycle counts and reconcile discrepancies to maintain high inventory accuracy.
- Interpretation: High accuracy indicates efficient inventory management, whereas frequent discrepancies might suggest issues in data handling or theft.
- Order Fulfillment Rate:
- Definition: The percentage of orders fulfilled correctly and on time to total orders received.
- Tracking: Monitor this KPI through the ERP or inventory management system to track order processing and delivery timelines.
- Interpretation: A high fulfillment rate signifies effective inventory and order management, impacting customer satisfaction positively.
- Lead Time Reduction:
- Definition: Measures the time taken from receiving an order to its delivery.
- Tracking: Analyze each segment of the lead time to identify bottlenecks or inefficiencies.
- Interpretation: Reduction in lead time typically means improved processes and faster response to market demands.
- Partner Satisfaction:
- Definition: Evaluates the contentment of partners regarding the inventory management and order fulfillment processes.
- Tracking: Use surveys and direct feedback mechanisms to gauge partner satisfaction.
- Interpretation: Higher satisfaction levels are indicative of successful collaboration and system efficiency.
Tracking these KPIs provides a comprehensive view of the operational health of the shared inventory system. By continuously monitoring these metrics, supply chain directors can make informed decisions, enhance operational efficiencies, and improve overall supply chain performance.
Overcoming Implementation Challenges in Real-Time Shared Inventory Systems
Implementing a real-time shared inventory platform in a multinational supply chain can encounter several challenges that may hinder progress. Understanding these obstacles and preparing solutions is crucial for a successful implementation. Below are common challenges and practical solutions to address them.
- Data Privacy and Security Concerns
Ensuring the security of shared data and complying with various national data protection regulations can be complex.
Solution: Implement robust encryption protocols and secure access controls. Regularly update security measures in line with current threats. Additionally, work closely with legal teams to ensure compliance with all applicable data protection laws. - Integration with Existing Systems
Integrating new software with legacy systems can be technically challenging and may disrupt existing operations.
Solution: Use middleware or customized APIs that facilitate seamless integration. Consider phased roll-outs to minimize disruption, and ensure thorough testing is conducted to address compatibility issues before full-scale implementation. - Resistance to Change
Resistance from staff or partners who are accustomed to existing processes can slow down or derail new system implementations.
Solution: Engage with all stakeholders early in the process through workshops and training sessions to demonstrate the benefits of the new system. Regular communication and transparency about the changes and benefits can also help in gaining their buy-in. - Scalability Issues
As the business grows, the platform might struggle to handle increased data volumes or additional partners.
Solution: Opt for scalable cloud-based solutions that can grow with the company’s needs. Regular scalability audits can help anticipate needs before they become issues. - Data Inconsistency and Errors
Inaccurate or inconsistent data from different sources can lead to poor decision-making.
Solution: Standardize data formats across all sources and implement automated data cleansing processes to maintain high data quality. Training users on the importance of data accuracy and consistency is also vital. - Cultural and Language Barriers
Multinational implementations may face hurdles due to cultural and language differences among various stakeholders.
Solution: Employ multilingual support teams and culturally sensitive training materials. Ensure that the system can handle multiple languages and cultural nuances in data representation.
By anticipating these challenges and preparing solutions ahead of time, companies can ensure smoother implementation of real-time shared inventory systems. Each solution should be tailored to the specific needs and conditions of the company, considering its technological, cultural, and operational contexts.
This blueprint offers a strategic pathway to streamline global inventory management. By adopting its guidelines, you can enhance operational efficiency, reduce costs, and improve collaboration across all supply chain partners, securing a robust competitive advantage in the global marketplace.
Unlock the full potential of your supply chain with SupplyChain360. Subscribe now for exclusive access to comprehensive blueprints, expert insights, and the resources you need to excel.