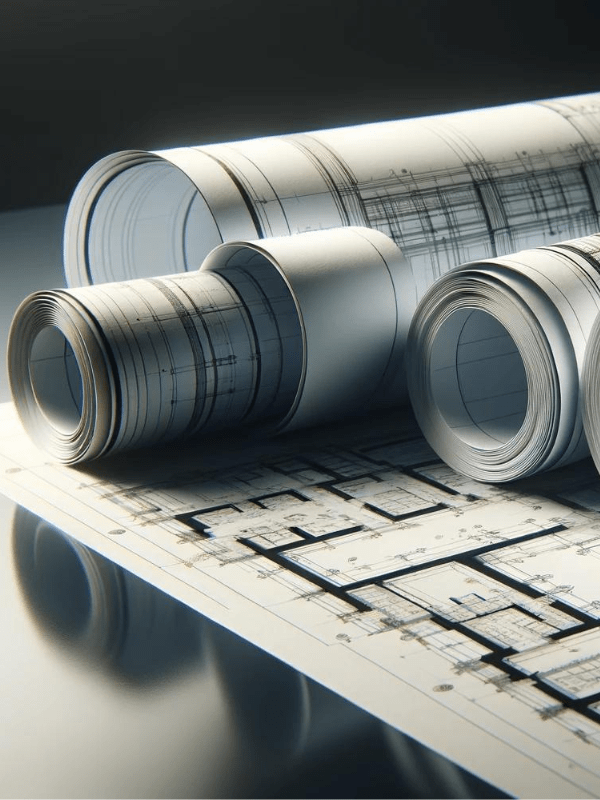
sustainability SERIES
Blueprints
In today’s global economy, sustainable supply chain management is not just a moral imperative but a strategic necessity. As companies face increasing scrutiny from consumers, regulators, and investors, the need to ensure that vendors comply with sustainability standards has never been more pressing. This blueprint addresses the critical challenges of assessing and enhancing vendor sustainability practices, offering a pathway to not only mitigate risks but also drive innovation and value creation. Embracing these strategies not only bolsters environmental and social governance but also positions companies for long-term success in an ever-evolving marketplace.
Read the full blueprint below >>
This blueprint presents a comprehensive guide for supply chain directors at multinational companies to effectively audit vendors for sustainability compliance, ensuring that their supply chains are not only efficient but also ethically and environmentally responsible. The main objective is to provide actionable insights and a step-by-step approach to enhance supply chain operations by integrating sustainability practices at every level.
Key value propositions include the ability to mitigate risks associated with non-compliance, improve brand reputation through responsible sourcing, and achieve cost savings through more efficient resource use. By adopting the strategies outlined in this blueprint, companies can navigate the complexities of global supply chains with confidence, ensuring compliance with international sustainability standards and driving long-term value creation.
The blueprint offers a detailed implementation guide, covering everything from defining sustainability criteria and developing assessment tools to conducting audits and leveraging technology for continuous improvement. With this toolkit, supply chain directors can transform their supply chains into models of sustainability and efficiency, setting a new standard for operational excellence in the modern business landscape.
In the context of supply chain management, particularly when auditing vendors for sustainability compliance, it is crucial to understand the foundational concepts and frameworks that guide these efforts. A primary concept underpinning this blueprint is the Triple Bottom Line (TBL), which emphasizes that true business success is measured not just by profit, but also by its impact on people (social equity) and the planet (environmental stewardship). This concept encourages companies to extend their responsibility beyond shareholders to include wider societal and environmental concerns, thus ensuring a more sustainable approach to business operations.
Incorporating TBL into supply chain management involves assessing vendors not only on cost and quality but also on their environmental practices and social implications. This broader evaluation criterion is essential for achieving a sustainable supply chain that minimizes environmental damage and promotes social welfare.
To operationalize these concepts, several sustainability frameworks have been developed. The Global Reporting Initiative (GRI) provides a comprehensive set of standards for reporting on environmental, social, and governance (ESG) impacts. It offers a framework for organizations to measure and communicate their sustainability performance, thereby helping supply chain directors to set clear expectations for their vendors and assess their compliance effectively.
Another key framework is the ISO 14001 Environmental Management System (EMS), which sets out criteria for an environmental management system. It provides a systematic approach for companies to improve their environmental performance through more efficient use of resources and reduction of waste. Implementing ISO 14001 can help businesses enhance their environmental sustainability while ensuring legal and regulatory compliance.
In practice, these frameworks assist companies in developing robust vendor auditing processes. By adopting these standards, businesses can create a structured approach to evaluate and improve their suppliers’ sustainability practices. This involves setting clear sustainability criteria, conducting thorough audits, and implementing continuous improvement mechanisms. Through these practical applications, supply chain directors can ensure that their vendors align with their sustainability objectives, thus contributing to a more responsible and sustainable global supply chain.
Implementing sustainability audits in supply chain operations requires a strategic approach that integrates best practices to ensure effectiveness and efficiency. Here are some of the best practices, along with illustrative examples and hypothetical scenarios:
- Establish Clear Sustainability Criteria: Begin by defining specific sustainability goals and standards that align with your company’s values and industry best practices. For example, a multinational clothing retailer might set criteria based on the use of organic materials, fair labor practices, and minimal water usage in production.
- Engage with Suppliers Early: Open communication with vendors about sustainability expectations and audit processes is crucial. A hypothetical scenario could involve a company organizing workshops or webinars for its suppliers to explain the audit process, sustainability criteria, and the importance of compliance, fostering a collaborative environment.
- Leverage Technology for Transparency: Implementing digital tools such as Supplier Relationship Management (SRM) systems can enhance transparency and efficiency. For instance, a food production company might use blockchain technology to trace the origin of ingredients, ensuring they meet sustainability standards.
- Conduct Regular Audits and Feedback Sessions: Regular audits are essential for monitoring compliance and continuous improvement. After each audit, it’s important to provide detailed feedback to suppliers, highlighting areas of success and those requiring improvement. Imagine a scenario where a tech company audits a supplier and discovers excessive energy usage; the company can then work with the supplier to implement energy-saving measures.
- Promote Continuous Improvement: Encourage suppliers to not only meet the set criteria but to continually seek ways to improve their sustainability practices. This could involve setting up an incentive program where suppliers that demonstrate significant sustainability improvements receive more favorable terms or recognition.
- Collaborate on Capacity Building: Help suppliers build their capacity to meet sustainability standards by sharing resources, knowledge, and best practices. For example, a large automotive company might partner with its suppliers to reduce carbon emissions by providing training on energy-efficient manufacturing techniques.
By adopting these best practices, companies can create a sustainable and resilient supply chain that not only complies with regulatory requirements and ethical standards but also contributes to long-term environmental and social well-being.
Implementing a robust vendor auditing process for sustainability compliance is a multifaceted endeavor that requires careful planning, execution, and continuous improvement. The following step-by-step guide is designed to provide a comprehensive and actionable approach.
Step 1: Define Sustainability Criteria
- Identify Core Sustainability Principles: Determine the key areas of sustainability that align with your company’s mission and values, such as environmental protection, social equity, and economic viability.
- Develop Specific Standards: Based on these principles, establish specific, measurable standards that vendors must meet, such as reducing carbon emissions, ensuring fair labor practices, or minimizing waste in manufacturing processes.
- Benchmark Against Industry Best Practices: Research and adopt recognized sustainability standards within your industry, leveraging frameworks like ISO 14001 or the Global Reporting Initiative (GRI) as references.
Step 2: Develop a Vendor Assessment Tool
- Create Assessment Templates: Design comprehensive templates that encompass all sustainability criteria, making it easy to evaluate vendor compliance during audits.
- Incorporate Quantitative and Qualitative Measures: Ensure the tool includes both measurable metrics (e.g., energy consumption levels) and qualitative assessments (e.g., labor conditions) to capture a full picture of vendor sustainability practices.
- Pilot the Tool: Test the assessment tool with a select group of vendors to refine its effectiveness and usability before full-scale implementation.
Step 3: Train Audit Teams
- Develop Training Programs: Create in-depth training programs for audit teams that cover sustainability principles, auditing techniques, and the use of the assessment tool.
- Focus on Communication Skills: Emphasize the importance of effective communication, especially in explaining the audit process and discussing findings with vendors.
- Conduct Regular Refresher Courses: Ensure audit teams stay updated on the latest sustainability practices and auditing methods through ongoing training sessions.
Step 4: Conduct Initial Vendor Audits
- Schedule Audits: Plan and communicate audit schedules well in advance to ensure vendor readiness and cooperation.
- Perform On-Site Evaluations: Whenever possible, conduct on-site evaluations to thoroughly assess manufacturing processes, working conditions, and environmental impact measures.
- Gather Comprehensive Data: Use the assessment tool to collect detailed information, supporting findings with documentation, interviews, and direct observations.
Step 5: Implement Continuous Monitoring and Feedback System
- Develop a Reporting System: Establish a clear reporting mechanism for audit results, highlighting areas of compliance, concern, and recommended improvements.
- Provide Constructive Feedback: Share audit findings with vendors in a manner that encourages dialogue and collaboration, focusing on areas for improvement and potential strategies for achieving compliance.
- Set Up Regular Review Meetings: Organize periodic meetings with vendors to discuss progress, address challenges, and update on changing sustainability standards or company requirements.
Step 6: Create Improvement Plans with Vendors
- Collaborate on Action Plans: Work together with vendors to develop tailored action plans for addressing areas of non-compliance, setting clear, achievable targets and timelines.
- Offer Support and Resources: Provide guidance, training, and possibly financial assistance to help vendors meet sustainability criteria, fostering a partnership approach to improvement.
- Monitor Progress: Regularly review vendor progress against the action plans, adjusting strategies as necessary to ensure continuous improvement.
Step 7: Integrate Findings into Strategic Decision-Making
- Analyze Audit Data: Systematically analyze the data collected from audits to identify trends, areas for improvement, and best practices within your supply chain.
- Inform Procurement Strategies: Use audit findings to inform your company’s procurement decisions, prioritizing vendors that meet or exceed sustainability standards and working to elevate those that fall short.
- Leverage for Stakeholder Engagement: Share success stories and challenges in sustainability auditing with internal and external stakeholders, using the insights to strengthen your company’s sustainability narrative.
Step 8: Foster a Culture of Sustainability
- Encourage Internal Engagement: Promote sustainability values within your organization, encouraging employees to contribute ideas and take part in sustainability initiatives.
- Expand Vendor Collaboration: Beyond auditing, work with vendors on joint sustainability projects or initiatives, leveraging collective resources and expertise to tackle larger environmental or social challenges.
- Stay Informed on Sustainability Trends: Keep abreast of emerging sustainability trends, technologies, and best practices, ready to adapt your auditing process and criteria to reflect the evolving landscape.
By following these steps, companies can establish a robust process for auditing vendors for sustainability compliance. This not only ensures that vendors adhere to environmental and social standards but also promotes a more sustainable, ethical, and resilient supply chain ecosystem.
The successful implementation of sustainability audits in supply chains relies heavily on the right mix of tools and technologies. These resources not only streamline the audit process but also enhance transparency, efficiency, and collaboration between companies and their vendors.
Supplier Relationship Management (SRM) Systems
Features: SRM systems offer a centralized platform to manage vendor information, performance metrics, and communication. They often include features for tracking compliance, conducting assessments, and managing contracts and procurement processes.
Benefits: By using SRM systems, companies can more effectively monitor and manage their relationships with vendors. These systems facilitate real-time visibility into vendor performance against sustainability criteria, making it easier to identify areas for improvement and track progress over time.
Integration: SRM systems can be integrated into the implementation steps by serving as the backbone for conducting audits, storing assessment templates, and recording audit results. They can also facilitate ongoing communication and collaboration with vendors, especially in developing and monitoring improvement plans.
Environmental Impact Assessment Tools
Features: These tools allow companies to quantify the environmental impact of their supply chain operations, including carbon footprint, water usage, and waste generation. They can range from simple calculators to comprehensive software that analyzes lifecycle impacts.
Benefits: With these tools, companies can gain a deeper understanding of the environmental impact of their products and services. This insight is crucial for setting realistic sustainability criteria and for making informed decisions that reduce environmental harm.
Integration: Environmental impact assessment tools can be used in the initial stages of the audit process to establish baseline measurements and identify key areas where vendors need to improve. They also play a role in continuous monitoring, helping to measure the effectiveness of implemented sustainability initiatives.
Blockchain Technology
Features: Blockchain offers a secure, transparent, and immutable ledger system that can track the provenance and lifecycle of products within the supply chain.
Benefits: The transparency provided by blockchain technology ensures that all stakeholders have access to verifiable information regarding the sustainability practices of vendors, from raw material sourcing to final product delivery.
Integration: In the context of sustainability audits, blockchain can be used to provide incontrovertible evidence of compliance with sustainability criteria, enhancing trust and reliability in vendor assessments. It can also support the continuous monitoring step by providing a real-time, tamper-proof record of vendor practices and improvements.
Incorporating these tools and technologies into the supply chain auditing process not only facilitates the practical aspects of conducting audits but also aligns with broader sustainability goals by promoting efficiency, transparency, and accountability.
For supply chain directors, defining and tracking the right Key Performance Indicators (KPIs) is crucial to effectively monitor and enhance the sustainability performance of their vendors. These metrics not only measure compliance but also guide continuous improvement efforts.
Environmental Impact KPIs
- Carbon Footprint: Measure the total greenhouse gas emissions (CO2e) produced directly and indirectly by a vendor. Tracking this KPI can help identify opportunities to reduce emissions through operational changes or innovations in the supply chain.
- Water Usage Efficiency: Evaluate the amount of water used per unit of production. This KPI is critical for assessing the sustainability of vendors, particularly in water-intensive industries, and for identifying water conservation opportunities.
- Waste Reduction Rate: Monitor the percentage reduction in waste generation over time. This KPI is essential for assessing the effectiveness of waste management and recycling initiatives.
Social Impact KPIs
- Labor Standards Compliance: Track adherence to fair labor practices, including working hours, child labor, and workplace safety. This KPI is vital for ensuring that vendors uphold ethical labor standards.
- Community Engagement: Measure the extent of vendor involvement in community development and social welfare projects. This KPI reflects the vendor’s commitment to social responsibility beyond its immediate business operations.
Operational and Governance KPIs
- Supplier Sustainability Score: Develop a composite score based on a vendor’s performance across various sustainability criteria. This score provides a holistic view of a vendor’s sustainability efforts and facilitates benchmarking against industry standards.
- Regulatory Compliance Rate: Track the percentage of vendors that comply with relevant environmental and social regulations. This KPI is crucial for mitigating legal and reputational risks associated with non-compliance.
Tracking and Interpretation
To effectively track these KPIs, supply chain directors should leverage the tools and technologies discussed earlier, such as SRM systems and environmental impact assessment tools. Regularly reviewing these metrics allows directors to identify trends, benchmark performance against industry standards, and pinpoint areas requiring intervention. Interpreting these metrics should involve a comprehensive analysis of both quantitative data and qualitative insights, enabling informed decision-making and strategic planning to enhance sustainability throughout the supply chain.
Tab contentIn navigating the complex terrain of global supply chains, this blueprint offers a structured and strategic approach to enhancing sustainability practices.
For FAQs for Auditing Vendors for Sustainability Compliance click here.
Subscribe to SupplyChain360 and take the next step in transforming your supply chain into a model of sustainability and efficiency!