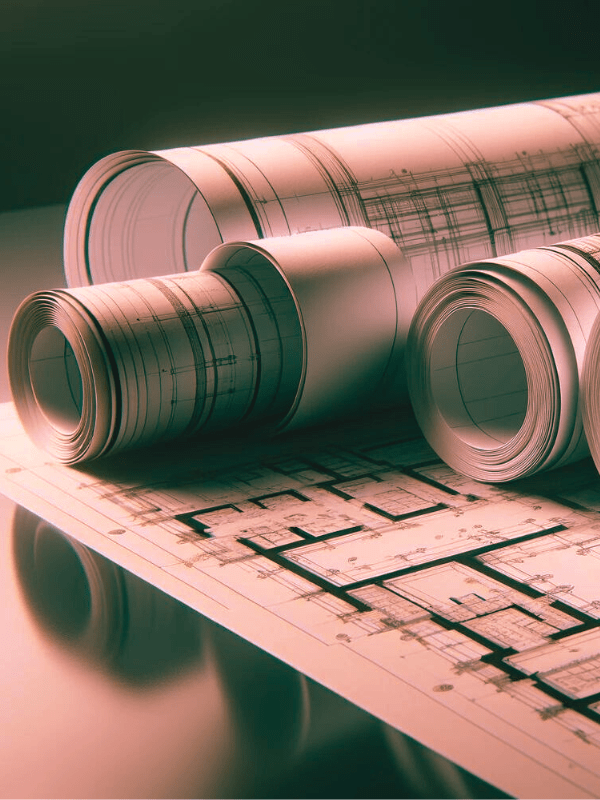
supply chain operations series
Technology & Data Analytics
BLUEPRINTS
Navigating the complexities of modern supply chains requires innovative solutions. This blueprint introduces and provides an integration roadmap for digital twins, offering a mirror to real-world supply chain operations with dynamic simulation capabilities.
Essential for those looking to enhance supply chain resilience, this guide provides a step-by-step approach to integrating digital twins, from initial assessment to full-scale implementation. By embracing this blueprint, businesses can achieve improved operational efficiency, reduced costs, and the agility to make informed decisions in the face of disruptions, securing a competitive edge in today’s volatile market.
This step-by-step guide outlines a structured approach to implementing digital twins within the supply chain. It emphasizes the importance of planning, data integration, model development, and continuous improvement, ensuring that the digital twin remains a valuable tool for enhancing supply chain resilience and decision-making.
Step 1: Assessment and Planning
Identify Critical Supply Chain Components
- Map out the entire supply chain, highlighting critical components such as key suppliers, logistics hubs, and manufacturing facilities.
Determine Objectives
- Define what you want to achieve with the digital twin, such as risk mitigation, efficiency improvement, or decision support.
Scope Definition
- Clearly delineate the scope of the digital twin, deciding whether it will cover the entire supply chain or focus on specific segments.
Stakeholder Engagement
- Engage with all relevant stakeholders to gather insights and ensure alignment with business objectives.
Feasibility Study
- Conduct a feasibility study to assess the technical and financial aspects of developing and implementing a digital twin.
Step 2: Data Collection and Integration
Data Identification
- List all types of data required, including operational, financial, environmental, and social data.
Data Sourcing
- Identify internal and external data sources, ensuring they are reliable and accessible.
Integration Framework
- Develop an integration framework that allows for the seamless aggregation of data from various sources, considering standards like ISA-95 for industrial data integration.
Data Quality Management
- Implement data quality management practices to ensure accuracy, completeness, and consistency of the data collected.
Real-time Data Capability
- Establish capabilities for real-time data collection and processing, using IoT devices and sensors where applicable.
Step 3: Digital Twin Development
Model Selection
- Choose the right modeling techniques (e.g., discrete event simulation, agent-based modeling) based on the complexity and dynamics of your supply chain.
Software and Platform Selection
- Select appropriate software and platforms that support scalability, interoperability, and real-time data processing.
Prototype Development
- Start with a prototype to validate the model with a subset of supply chain operations.
Validation and Testing
- Validate the digital twin model against real-world outcomes to ensure accuracy, using techniques like parallel runs or historical data comparison.
Scalability and Flexibility
- Ensure the digital twin design is scalable to accommodate future expansion and flexible enough to adapt to changes in the supply chain.
Step 4: Simulation and Analysis
Scenario Planning
- Use the digital twin to simulate various scenarios, including supply disruptions, demand fluctuations, and changes in logistics.
Risk Assessment
- Identify and assess potential risks in the supply chain using the digital twin, focusing on their likelihood and impact.
Decision Support
- Leverage the digital twin for decision support, providing insights into optimal decisions under various scenarios.
Performance Optimization
- Utilize simulation results to identify opportunities for efficiency improvements and cost reductions in the supply chain.
Iterative Analysis
- Regularly update and rerun simulations to reflect changes in the supply chain or external environment.
Step 5: Implementation and Iteration
Integration with Operations
- Integrate the digital twin with day-to-day operations, ensuring it becomes an integral part of the decision-making process.
Training and Change Management
- Develop comprehensive training programs to ensure that staff understand how to use the digital twin effectively.
Feedback Loop
- Establish a feedback loop to collect input from users and stakeholders, using this to inform ongoing improvements to the digital twin.
Continuous Improvement
- Adopt a continuous improvement approach, using the digital twin to regularly identify and implement enhancements to supply chain operations.
Future-proofing
- Regularly review and update the digital twin to incorporate new technologies, methodologies, and changes in the business environment.
Each step, from assessment to implementation, builds upon the previous one, ensuring a comprehensive and cohesive strategy for integrating digital twins into supply chain operations. By following this guide, supply chain directors can effectively leverage digital twins to navigate the complexities of the modern supply chain landscape.
Implementing digital twins within supply chain operations requires not just a strategic approach but also adherence to best practices that ensure success and sustainability. Here are key practices to follow:
- Stakeholder Collaboration: Foster a collaborative environment where IT, operations, supply chain managers, and other stakeholders work together. This synergy is crucial for aligning the digital twin’s objectives with the overall business strategy and ensuring that all perspectives are considered in its development and implementation.
- Incremental Implementation: Start small by focusing on a specific segment of the supply chain or a particular challenge. This approach allows for manageable pilot projects that can demonstrate value and provide learnings to inform broader implementation.
- Comprehensive Data Strategy: Develop a robust data management strategy that encompasses data collection, storage, analysis, and security. Ensure that the data feeding into the digital twin is of high quality and reflects the real-time status of the supply chain to maintain the accuracy and reliability of simulations and predictions.
- User Training and Support: Invest in extensive training programs for users at all levels to ensure they understand how to interact with and leverage the digital twin. Continuous support and knowledge sharing are essential to encourage adoption and innovative use of the system.
- Iterative Development and Feedback Loops: Treat the digital twin as a living model that evolves. Regularly update it to reflect changes in the supply chain, feedback from users, and advancements in technology. An iterative approach facilitates continuous improvement and adaptation to new challenges and opportunities.
- Integration with Existing Systems: Ensure seamless integration of the digital twin with existing supply chain management systems, ERP systems, and other operational tools. This integration is critical for enabling real-time data exchange and ensuring that the digital twin is a complementary tool rather than an isolated solution.
- Focus on Scalability and Flexibility: Design the digital twin with scalability in mind to accommodate future growth and changes in the supply chain. Flexibility is also key to adapting to new market conditions, technologies, and business models.
By following these best practices, companies can maximize the benefits of digital twins in their supply chain operations, driving efficiency, resilience, and innovation.
For successful digital twin implementation in supply chain operations, selecting the right tools and technologies is critical. These resources not only facilitate the creation and maintenance of digital twins but also ensure their effective integration and utilization within the existing supply chain infrastructure.
- IoT Devices and Sensors: These are foundational for real-time data collection, providing the necessary input for digital twins to accurately reflect physical assets and processes. They enable dynamic updates to the digital twin and enhance decision-making with real-time data.
- Cloud Computing Platforms: Cloud services offer the scalability and flexibility needed for digital twin implementations. Benefits include cost efficiency, scalability, and the facilitation of collaboration across global teams.
- Data Analytics and AI: Advanced analytics and artificial intelligence tools are pivotal for interpreting the vast amounts of data generated by digital twins. They enable predictive analytics, anomaly detection, and optimization algorithms that drive proactive decision-making.
- Simulation Software: This technology allows for the creation of detailed models that can simulate various supply chain scenarios. Features include scenario planning, risk assessment, and system optimization.
- Integration Platforms: Middleware and integration platforms ensure that digital twins can communicate effectively with existing ERP, SCM, and CRM systems. This connectivity is crucial for the seamless flow of data across the supply chain ecosystem.
- Cybersecurity Solutions: Given the reliance on data and interconnected systems, robust cybersecurity measures are indispensable to protect sensitive data and maintain the integrity of the digital twin against cyber threats.
By leveraging these tools and technologies, companies can create comprehensive and accurate digital twins that serve as powerful instruments for supply chain analysis, optimization, and resilience. Their integration into the supply chain not only enhances operational visibility and agility but also drives innovation and competitive advantage.
For supply chain directors leveraging digital twins, identifying and monitoring the right metrics and Key Performance Indicators (KPIs) is crucial to measure the success and value of these implementations. Here’s a concise overview of essential metrics:
- Supply Chain Visibility: Measures the extent to which products, materials, and information can be monitored throughout the supply chain, enhanced by the real-time digital representation provided by digital twins.
- Response Time to Disruptions: Tracks the time taken from the identification of a disruption to the implementation of a corrective action, showcasing the agility provided by digital twin insights.
- Inventory Accuracy: Involves comparing digital twin data with physical counts to ensure the reliability of inventory management enhanced by real-time digital twin data.
- Operational Efficiency: Encompasses improvements in production throughput, order fulfillment times, and transportation costs, driven by digital twin optimizations.
- Cost Reduction: Identifies cost-saving opportunities across the supply chain, from logistics to production, highlighted by scenario simulations through digital twins.
- Risk Mitigation: Measures the effectiveness of risk management strategies, such as reduced stockouts or improved supplier reliability, enabled by digital twins.
Tracking these KPIs involves integrating digital twin data with supply chain management systems to enable real-time monitoring and analysis. Supply chain directors should regularly review these metrics, using dashboards and analytical tools, to make informed decisions and continuously refine their supply chain strategies for optimal performance.
Implementing digital twins in supply chain operations presents several challenges, each requiring strategic solutions to ensure successful adoption and maximization of benefits. Here are common obstacles and practical approaches to address them:
- High Initial Investment:
The development and deployment of digital twins can require significant upfront costs. Solution: Focus on demonstrating the ROI through pilot projects, highlighting long-term savings and efficiency gains.
- Data Complexity and Volume:
The sheer amount of data for an accurate digital twin can be overwhelming. Solution: Implement robust data management platforms that can handle large volumes of data, starting with critical data points.
- Integration with Existing Systems:
Ensuring seamless work with current systems can be complex. Solution: Adopt middleware and integration platforms that facilitate seamless data exchange and involve IT teams early in the planning stage.
- Skills and Expertise:
Deployment requires a team with diverse skills. Solution: Invest in training and development programs to upskill existing staff and consider hiring specialists or partnering with external consultants.
- Change Resistance:
Resistance among employees can hinder adoption. Solution: Implement change management strategies, including clear communication of benefits and inclusive training programs.
- Scalability and Flexibility:
Digital twins need to adapt to changing conditions. Solution: Design with scalability in mind, using modular architectures and regularly update the digital twin to align with supply chain changes.
- Cybersecurity and Data Privacy:
Increased connectivity raises concerns about security and privacy. Solution: Employ advanced cybersecurity measures, including encryption and access controls, and ensure compliance with data protection regulations.
By anticipating these challenges and implementing the suggested solutions, supply chain directors can navigate the complexities of digital twin adoption, ensuring a smoother integration and enhanced supply chain resilience.
This blueprint is your roadmap to fortifying supply chain resilience through digital twin technology. Embrace it to unlock enhanced operational efficiency, cost reduction, and strategic agility, ensuring your supply chain withstands disruptions and thrives in the competitive landscape of tomorrow.
Unlock the full potential of your supply chain! Subscribe to SupplyChain360 now for exclusive access to more blueprints, resources, and cutting-edge strategies designed to drive your success.