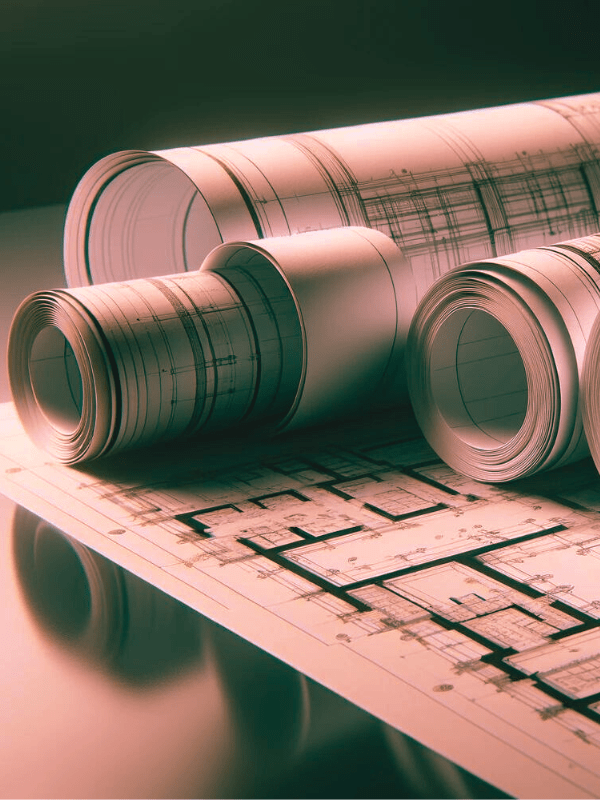
Supply Chain operations series
Collaboration & Compliance
BLUEPRINTS
Synchronizing production schedules across multinational organizations presents significant challenges, misaligned operations can lead to inefficiencies that affect the bottom line.
This blueprint provides a structured approach to harmonize production timelines, ensuring seamless operations and optimized resource utilization. By integrating advanced tools and methodologies, it addresses specific challenges inherent in managing diverse and geographically dispersed teams.
Adopting this blueprint enables organizations to enhance operational efficiency, reduce waste, and improve delivery times, providing a competitive edge in a rapidly evolving business landscape.
Step-by-Step Guide: Implementing Synchronized Production Schedules
This detailed guide serves as the centerpiece of the blueprint for synchronizing production schedules across multinational organizations. Each step is designed to be actionable, supported by modern management models and technologies, ensuring that supply chain directors can effectively implement and benefit from a unified scheduling strategy.
Step 1: Assessment of Current Production Schedules
Gather Data
- Collect detailed production schedules from all global units, including start and end times, resources used, and output levels.
Analysis Tools
- Utilize advanced analytics platforms to process and visualize overlapping schedules and identify inefficiencies and bottlenecks.
Stakeholder Engagement
- Organize workshops with key stakeholders across different regions to gather insights on operational impact and practical challenges.
Step 2: Design of a Synchronized Schedule Framework
Model Selection
- Evaluate and select a scheduling model like Just-In-Time (JIT) or Theory of Constraints (TOC), considering factors such as product type, production flow, and market demand.
Framework Development
- Build a tailored framework that aligns with corporate strategy, integrates local variations, and scales across global operations. Include contingency planning for disruptions.
Technology Integration
- Plan the phased integration of ERP and APS systems, detailing necessary customizations to support complex, multi-location scheduling and real-time adjustments.
Step 3: Technology and Tools Deployment
ERP System Customization
- Configure the ERP system to accurately reflect and manage the new synchronized schedules, enhancing features for scalability and cross-functional data sharing.
APS System Implementation
- Implement an APS that utilizes machine learning to predict potential scheduling conflicts and automatically suggest optimal adjustments.
Training Programs
- Develop a comprehensive training program using interactive modules and real-time simulations to ensure all users are proficient with new tools and processes.
Step 4: Pilot Testing of the Synchronized Schedule
Selection Criteria for Pilot Locations
- Select locations based on their strategic importance, diversity in operations, and historical challenges with scheduling.
Implementation of Pilot Schedules
- Execute the synchronized schedules, integrating real-time data feeds to monitor performance and system responsiveness.
Metrics and Evaluation
- Establish a robust framework of metrics such as cycle time reduction, improvement in workforce utilization, and decrease in inventory costs to evaluate the pilot.
Step 5: Evaluation and Iterative Improvement
Data-Driven Performance Review
- Utilize advanced data analytics to assess pilot outcomes against set KPIs, analyzing areas for improvement and scalability.
Feedback Loops
- Create structured feedback sessions with pilot participants to gather qualitative and quantitative feedback, facilitating iterative refinements.
Refinement and Optimization
- Apply continuous improvement methodologies, such as Kaizen or Six Sigma, to refine scheduling processes based on pilot feedback and analytical insights.
Step 6: Full-scale Implementation
Roll-out Strategy
- Develop a detailed roll-out strategy that includes timeline, resource allocation, and risk mitigation measures for a full-scale implementation.
Real-Time Monitoring
- Implement a dashboard for real-time monitoring of key production metrics across all locations to ensure alignment and prompt resolution of scheduling discrepancies.
Continuous Improvement Protocol
- Establish protocols for ongoing review and optimization of the scheduling system, incorporating new technologies and methodologies as they arise.
Step 7: Long-term Management and Scalability
Sustainability Integration
- Embed sustainability metrics into the scheduling framework to monitor and optimize energy use and waste management.
Scalability Audits
- Regularly conduct scalability audits to assess the system’s capacity to handle new products, markets, and changes in production volume.
Future-proofing Initiatives
- Stay ahead of industry trends and technological advancements, planning for future integrations that enhance scheduling flexibility and resilience.
This comprehensive approach ensures that the implementation of synchronized production schedules is effective, scalable, and sustainable, addressing the unique challenges and opportunities of multinational organizations.
Implementing best practices within supply chain operations is essential for enhancing efficiency, reducing costs, and improving overall performance. Here are key actionable guidelines to consider when applying the principles of the blueprint:
- Collaborative Planning: Foster a collaborative environment across all levels of the supply chain. Encourage communication between suppliers, manufacturers, and distributors to align objectives and synchronize activities.
- Lean Inventory Management: Adopt lean inventory techniques to minimize waste and optimize inventory levels. Techniques like Just-In-Time (JIT) delivery can reduce holding costs and free up working capital.
- Integrated Technology Systems: Leverage integrated technology systems that enhance visibility and coordination across the supply chain. Tools like ERP and cloud-based supply chain management software provide real-time data, allowing for quicker decision-making.
- Continuous Improvement: Establish a culture of continuous improvement by regularly assessing supply chain processes and identifying areas for enhancement. Use metrics and KPIs to track performance and implement improvement methodologies like Six Sigma or Kaizen.
- Risk Management: Develop a comprehensive risk management plan that identifies potential risks within the supply chain. Implement strategies such as diversifying supplier base and having contingency plans for critical parts of the supply chain.
- Sustainability Practices: Integrate sustainability into supply chain operations by optimizing transportation routes, using eco-friendly materials, and ensuring compliance with environmental regulations.
- Training and Development: Invest in training programs to ensure that staff at all levels are knowledgeable about the latest supply chain practices and technologies. Regular training updates can help maintain a competitive edge.
By following these best practices, organizations can improve their supply chain operations, leading to increased operational efficiency, better customer satisfaction, and a stronger competitive position in the market.
Implementing synchronized production schedules in multinational supply chains presents unique challenges. This section outlines common obstacles and provides actionable solutions to ensure successful implementation of the blueprint:
- Resistance to Change:
Implement comprehensive change management strategies. Start with clear communication about the benefits of the new system. Provide extensive training and support to ease the transition, and actively involve employees in the implementation process to gain their buy-in and reduce resistance.
- Technological Integration:
Conduct a thorough IT audit to assess current capabilities and identify gaps. Choose modular, scalable technologies that can be integrated seamlessly with existing systems. Engage with experienced IT consultants to guide the integration process and provide ongoing support.
- Data Accuracy and Consistency:
Standardize data collection and management processes across all locations. Implement centralized data management systems, such as cloud-based ERP systems, to maintain consistency. Regularly train staff on data entry and maintenance best practices.
- Supply Chain Visibility:
Leverage advanced supply chain management platforms that offer real-time tracking and analytics. Employ IoT devices to enhance visibility at every stage of the supply chain. Regularly review and update supply chain maps to reflect changes and ensure transparency.
- Regulatory Compliance:
Establish a dedicated regulatory compliance team to stay updated on international trade laws and regulations. Implement compliance management software to track changes and ensure adherence at all operational levels.
- Scalability and Flexibility:
Design systems with scalability in mind, using technologies that can adapt to increased demands or changes in the business environment. Regularly conduct strategic reviews to adapt processes and incorporate new technologies or methodologies that enhance flexibility.
- Cultural Differences:
Promote cultural awareness and sensitivity training programs. Establish clear, universal communication protocols to minimize misunderstandings and align operations across diverse teams.
By anticipating these challenges and implementing these solutions, organizations can enhance their ability to successfully implement synchronized production schedules, leading to more streamlined and efficient supply chain operations.
For supply chain directors, defining and tracking key performance indicators (KPIs) is crucial for assessing the effectiveness of synchronized production schedules across multinational organizations. Here are essential metrics to measure success:
- On-Time Delivery (OTD): Assess the percentage of shipments delivered on or before the promised date.
Tracking: Utilize ERP systems to regularly record and analyze delivery times versus expectations.
- Cycle Time: Measures the total time from initiation to completion of production.
Tracking: Use time-tracking software integrated into production lines to analyze trends and outliers.
- Inventory Turns: Indicates how often inventory is sold and replaced over a period.
Tracking: Calculate this KPI using inventory management software by dividing the cost of goods sold by average inventory value.
- Capacity Utilization: Measures how well productive capacity is being used.
Tracking: Monitor output through data analytics tools and compare it against maximum capacity.
- Lead Time: Interval between the initiation and completion of a production process.
Tracking: Analyze procurement, production, and delivery times using APS systems for accuracy and timeliness.
- Customer Satisfaction: Customer feedback on product quality and delivery service.
Tracking: Use CRM systems to gather and analyze customer satisfaction surveys and feedback.
These KPIs offer a comprehensive view of the operational efficiency and effectiveness of synchronized production schedules. By consistently tracking and interpreting these metrics, supply chain directors can optimize processes, improve decision-making, and ultimately enhance overall organizational performance.
Overcoming Implementation Challenges in Real-Time Shared Inventory Systems
Implementing a real-time shared inventory platform in a multinational supply chain can encounter several challenges that may hinder progress. Understanding these obstacles and preparing solutions is crucial for a successful implementation. Below are common challenges and practical solutions to address them.
- Data Privacy and Security Concerns
Ensuring the security of shared data and complying with various national data protection regulations can be complex.
Solution: Implement robust encryption protocols and secure access controls. Regularly update security measures in line with current threats. Additionally, work closely with legal teams to ensure compliance with all applicable data protection laws. - Integration with Existing Systems
Integrating new software with legacy systems can be technically challenging and may disrupt existing operations.
Solution: Use middleware or customized APIs that facilitate seamless integration. Consider phased roll-outs to minimize disruption, and ensure thorough testing is conducted to address compatibility issues before full-scale implementation. - Resistance to Change
Resistance from staff or partners who are accustomed to existing processes can slow down or derail new system implementations.
Solution: Engage with all stakeholders early in the process through workshops and training sessions to demonstrate the benefits of the new system. Regular communication and transparency about the changes and benefits can also help in gaining their buy-in. - Scalability Issues
As the business grows, the platform might struggle to handle increased data volumes or additional partners.
Solution: Opt for scalable cloud-based solutions that can grow with the company’s needs. Regular scalability audits can help anticipate needs before they become issues. - Data Inconsistency and Errors
Inaccurate or inconsistent data from different sources can lead to poor decision-making.
Solution: Standardize data formats across all sources and implement automated data cleansing processes to maintain high data quality. Training users on the importance of data accuracy and consistency is also vital. - Cultural and Language Barriers
Multinational implementations may face hurdles due to cultural and language differences among various stakeholders.
Solution: Employ multilingual support teams and culturally sensitive training materials. Ensure that the system can handle multiple languages and cultural nuances in data representation.
By anticipating these challenges and preparing solutions ahead of time, companies can ensure smoother implementation of real-time shared inventory systems. Each solution should be tailored to the specific needs and conditions of the company, considering its technological, cultural, and operational contexts.
This blueprint equips you with the tools and strategies necessary to streamline and synchronize production schedules across your multinational organization, leading to improved efficiency, reduced costs, and a stronger competitive position in the global market.
Unlock the full potential of your supply chain with SupplyChain360. Subscribe now for exclusive access to comprehensive blueprints, expert insights, and the resources you need to excel.