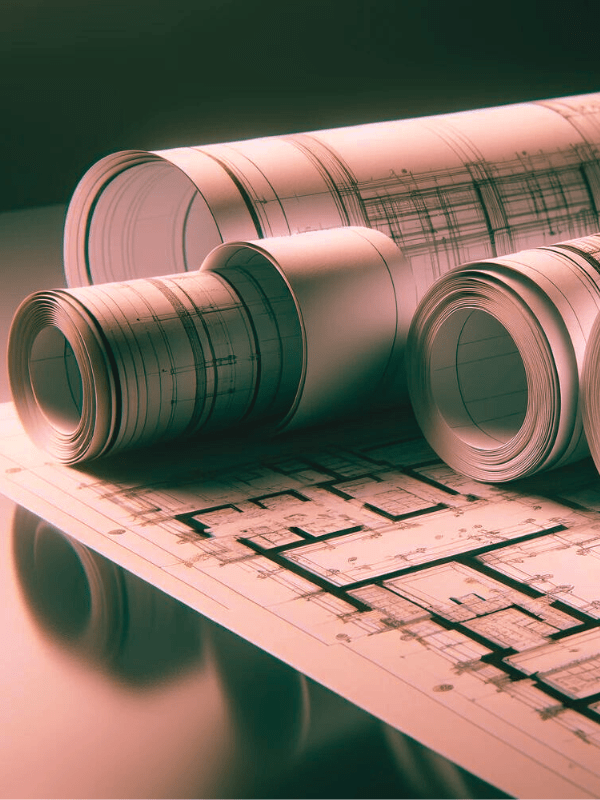
Supply Chain operations series
Warehouse Optimization
BLUEPRINTS
In today’s competitive market, efficient order processing is critical. Integrating smart picking technologies addresses this challenge, significantly enhancing speed and accuracy in supply chain operations.
This blueprint provides a structured approach to adopting these advanced technologies, crucial for maintaining competitive advantage and improving operational efficiency.
It details a step-by-step implementation strategy, ensuring seamless integration with minimal disruption. By adopting the practices outlined, companies can expect reduced operational costs, improved worker productivity, and enhanced customer satisfaction.
Leverage this blueprint to transform your supply chain operations and achieve a sustainable competitive edge.
This section outlines a detailed, step-by-step process to successfully implement smart picking technologies in large, multinational supply chain operations. Each step includes specific actions, models, and decision-making frameworks to guide supply chain directors through the integration process.
Step 1: Initial Assessment and Needs Analysis
Conduct a Comprehensive Current State Analysis
- Map existing order picking and fulfillment processes using tools such as process flow diagrams and value stream mapping to identify bottlenecks and inefficiencies.
Define Objectives and Scope
- Establish clear objectives for integrating smart picking technologies, such as reducing picking time by X% or improving accuracy by Y%.
Assess Technological and Operational Readiness
- Evaluate current technological infrastructure and operational practices to determine readiness for integration using SWOT (Strengths, Weaknesses, Opportunities, Threats) analysis.
Stakeholder Engagement
- Identify key stakeholders and involve them early in the project to gather insights and align objectives.
Step 2: Technology Selection
Market Research
- Perform comprehensive research to identify available smart picking technologies that fit the company’s specific needs.
Vendor Evaluation and Selection
- Use a weighted scoring model to assess and compare vendors based on criteria such as technology maturity, support services, integration capabilities, and cost.
Pilot Testing
- Select a small scale or section of operations to test the technologies to assess their impact and suitability before full-scale deployment.
Step 3: System Integration Planning
Integration Design
- Develop a detailed integration plan that includes timelines, resources, and specifications. Utilize project management methodologies like Agile for iterative testing and implementation.
Compatibility Checks
- Ensure that new technologies are compatible with existing WMS and ERP systems, potentially involving middleware or customized APIs.
Risk Management Planning
- Implement a risk management framework to identify, assess, and mitigate potential risks associated with technology integration.
Step 4: Implementation
Infrastructure Modification
- Make necessary modifications to warehouse layouts and infrastructure to accommodate new technologies, guided by principles of lean management to optimize space and flow.
Technology Installation
- Oversee the installation of technologies, ensuring adherence to technical specifications and safety standards.
System Integration and Testing
- Integrate new technologies with existing systems and conduct thorough testing to ensure functionality and performance metrics are met.
Step 5: Training and Change Management
Develop Training Programs
- Create comprehensive training programs for all affected staff, focusing on how to operate new technologies and adapt to new processes.
Change Management
- Apply change management principles to assist employees in adapting to technological changes, using models such as ADKAR (Awareness, Desire, Knowledge, Ability, Reinforcement).
Feedback Loops
- Establish feedback mechanisms to monitor usage and acceptance of new technologies among staff.
Step 6: Go-Live and Monitoring
Go-Live
- Execute a phased or full rollout of the technology across operations.
Continuous Monitoring
- Utilize real-time monitoring tools to track performance against KPIs established in the initial assessment phase.
Ongoing Support and Troubleshooting
- Provide ongoing support and immediate troubleshooting to address any operational issues post-implementation.
Step 7: Post-Implementation Review and Optimization
Performance Review
- Conduct a comprehensive review of the technology’s impact on order processing efficiency and accuracy.
Lessons Learned
- Document lessons learned and apply these insights to future phases of technology integration or other projects.
Continuous Improvement
- Leverage continuous improvement frameworks like Six Sigma to refine and optimize technology usage based on data gathered during monitoring.
This structured guide ensures that the integration of smart picking technologies is approached methodically, leveraging modern management frameworks and thorough planning to achieve enhanced operational efficiency.
Implementing smart picking technologies requires more than just technological integration; it involves strategic planning, effective management, and continuous improvement. Here are some key best practices to ensure successful deployment and operation within supply chain frameworks:
- Strategic Planning
- Align Technology with Business Goals: Ensure that the selected smart picking solutions directly contribute to the strategic objectives of the company, such as increasing operational efficiency, reducing costs, or improving customer satisfaction.
- Comprehensive Project Management: Adopt a structured project management approach, such as PRINCE2 or PMBOK, to manage the integration process from start to finish, ensuring that all aspects of the project are covered systematically.
- Effective Management
- Stakeholder Involvement: Engage all relevant stakeholders from the onset, including suppliers, employees, and customers where appropriate, to ensure their needs and concerns are addressed, and they are supportive of the changes.
- Change Management: Utilize established change management frameworks like Kotter’s 8-Step Change Model to manage the human aspect of technology integration, ensuring smooth transition and adoption by all users.
- Operational Excellence
- Optimization of Layout and Design: Redesign the warehouse layout to accommodate the new technologies, optimizing the flow of goods and minimizing travel times and bottlenecks.
- Regular Training and Development: Conduct regular training sessions and provide up-to-date materials to keep staff proficient in using new technologies and methodologies.
- Quality and Continuous Improvement
- Quality Assurance: Implement stringent quality controls and regular audits to ensure the technology performs as expected without disrupting existing operations.
- Lean Six Sigma: Adopt Lean Six Sigma methodologies to continuously improve process efficiency, reduce waste, and eliminate defects in processes that involve the smart picking technologies.
- Scalability and Future-Proofing
- Scalability Considerations: Plan for future growth by choosing technologies that can be scaled up easily and integrated with other emerging technologies.
- Stay Updated with Technological Advancements: Keep abreast of developments in smart picking technologies and related fields to continually enhance and update the technology stack as necessary.
By following these best practices, companies can maximize the benefits of integrating smart picking technologies, ensuring they are effectively adapted to the unique challenges and opportunities of their supply chain operations.
Successfully implementing smart picking technologies in supply chain operations requires the use of specific tools and systems that enhance efficiency and accuracy. Here’s an overview of key technologies and their integration into the previously outlined implementation steps:
- Automated Storage and Retrieval Systems (ASRS)
- Features: ASRS are high-density storage solutions that automatically place and retrieve loads from defined storage locations.
- Benefits: They significantly reduce manual labor, improve inventory accuracy, and enhance space utilization.
- Integration: During the infrastructure modification phase, ASRS can be integrated with existing warehouse management systems to streamline operations and optimize storage.
- Robotics and Autonomous Mobile Robots (AMRs)
- Features: Robotics in warehouses include robotic arms and AMRs that assist in picking and transporting items within facilities.
- Benefits: These robots speed up the picking process, reduce human error, and can operate in environments that might be challenging for humans.
- Integration: In the technology installation step, robotics can be configured to work in tandem with existing systems and can be scaled up as needed to meet increased demands.
- Wearable Technology
- Features: This includes smart glasses and wearable scanners that provide hands-free operations for workers.
- Benefits: Wearables enhance picking accuracy and speed as workers receive real-time information directly in their line of sight, which reduces the time spent on manual data entry and lookup.
- Integration: During the training and change management phase, wearable technologies can be introduced to staff to facilitate a smoother transition to technology-enhanced processes.
- Voice-Directed Picking Systems
- Features: These systems use voice commands to direct pickers to the correct warehouse locations and verify picks verbally.
- Benefits: Voice picking increases productivity and accuracy while allowing workers to keep their eyes and hands free for picking tasks.
- Integration: These systems should be tested during the pilot testing stage to fine-tune the integration with the warehouse’s existing ERP systems and to ensure that they meet the desired improvements in pick rates and accuracy.
- IoT Sensors and RFID
- Features: Sensors and RFID tags can track products throughout the warehouse in real-time.
- Benefits: They provide accurate, real-time inventory data, reduce losses, and enhance the reorder processes.
- Integration: Implement IoT sensors during the system integration planning to ensure seamless data flow between the smart picking technologies and the warehouse management software.
These technologies, when properly integrated following the strategic steps of the implementation guide, will collectively elevate the efficiency and effectiveness of supply chain operations, paving the way for a future-proof, scalable logistics environment.
For supply chain directors to accurately measure the success of smart picking technology integrations, certain key performance indicators (KPIs) should be closely monitored. These metrics not only provide insight into operational efficiency but also help in assessing the return on investment and overall improvement in supply chain processes.
- Pick Accuracy
- Definition: Measures the accuracy of order picking operations by comparing the number of correctly picked orders against total orders.
- Tracking and Interpretation: Track through scanning systems integrated with WMS; high accuracy rates indicate effective use of smart picking technologies.
- Order Cycle Time
- Definition: The total time taken from when an order is placed to when it is fully processed and ready for shipment.
- Tracking and Interpretation: Monitor using time-stamp data in the ERP system; reductions in cycle time post-implementation signify improved operational speed.
- Inventory Shrinkage Rate
- Definition: Represents the percentage of inventory loss due to errors, theft, or damage during the picking process.
- Tracking and Interpretation: Calculate by comparing physical inventory counts to inventory records; a lower shrinkage rate post-implementation reflects better inventory control and accuracy.
- Labor Utilization
- Definition: Assesses the efficiency of labor use by measuring the amount of labor time spent actively picking orders versus total available labor time.
- Tracking and Interpretation: Analyze through labor management systems integrated with picking technologies; improvements in labor utilization rates suggest more effective labor deployment.
- Return on Investment (ROI)
- Definition: Measures the financial return on the investment made in smart picking technologies relative to the cost.
- Tracking and Interpretation: Calculate by dividing the net benefits (cost savings and increased revenue) by the total cost of the smart picking technologies; a positive ROI indicates financial success of the implementation.
By effectively tracking and interpreting these KPIs, supply chain directors can make informed decisions about the ongoing use and future enhancements of smart picking technologies in their operations. These metrics serve as a critical part of the feedback loop in continuous improvement strategies.
Implementing smart picking technologies in multinational supply chain operations presents several challenges. Below are the most common hurdles encountered, along with practical solutions to help ensure successful integration and operation.
- High Initial Investment Costs
Challenge: Smart picking systems, such as automated robots and advanced software, require a substantial initial investment, which can be prohibitive.
Solution: To mitigate this, companies should consider phased implementation, starting with pilot projects that demonstrate ROI before full deployment. Additionally, exploring financing options or leasing hardware can reduce upfront costs. - Integration with Existing Systems
Challenge: Integrating new technologies with existing warehouse management and ERP systems can be complex, risking disruptions to current operations.
Solution: Employ middleware solutions that act as a bridge between new technologies and existing systems, ensuring smooth data flow and functionality. Involve IT teams early in the planning process for technical feasibility assessments. - Resistance to Change from Staff
Challenge: Employees may resist new technologies due to fear of job displacement or the learning curve associated with new systems.
Solution: Engage in proactive communication and training programs that outline the benefits of smart picking technologies, not only for the company but for the employees’ work environment. Establish a change management plan that includes incentives and clear career advancement paths. - Technical Issues and Downtime
Challenge: Initial technical glitches and system downtimes can disrupt operations and lead to skepticism about the new systems’ reliability.
Solution: Choose technology vendors with robust support and maintenance agreements. Implement comprehensive training for the in-house IT team to handle minor issues quickly. Schedule regular system audits and updates to minimize downtime. - Data Security and Privacy Concerns
Challenge: Implementing technologies that rely on data collection and real-time tracking can raise concerns about data security and privacy.
Solution: Ensure that all technologies comply with international data protection regulations. Implement best practices in cybersecurity, such as encrypted data transmissions and secure access controls. Regularly review and update security protocols. - Scalability and Future Growth
Challenge: Technologies might not scale with business growth, leading to additional replacements or upgrades that increase costs.
Solution: Opt for modular technologies that easily integrate with other systems and can be scaled up as needed. Plan for future needs during the initial selection process, considering potential business expansions or changes in operation scale.
By anticipating these challenges and preparing solutions in advance, companies can enhance their chances of a smooth and successful implementation of smart picking technologies. This proactive approach not only addresses immediate hurdles but also paves the way for sustained operational success.
This blueprint offers a clear path to integrating smart picking technologies, significantly boosting efficiency and accuracy in your supply chain operations. Implement these strategies to enhance productivity, reduce costs, and stay competitive in a rapidly evolving marketplace.
Unlock the full potential of your supply chain with SupplyChain360. Subscribe now for exclusive access to comprehensive blueprints, expert insights, and the resources you need to excel.