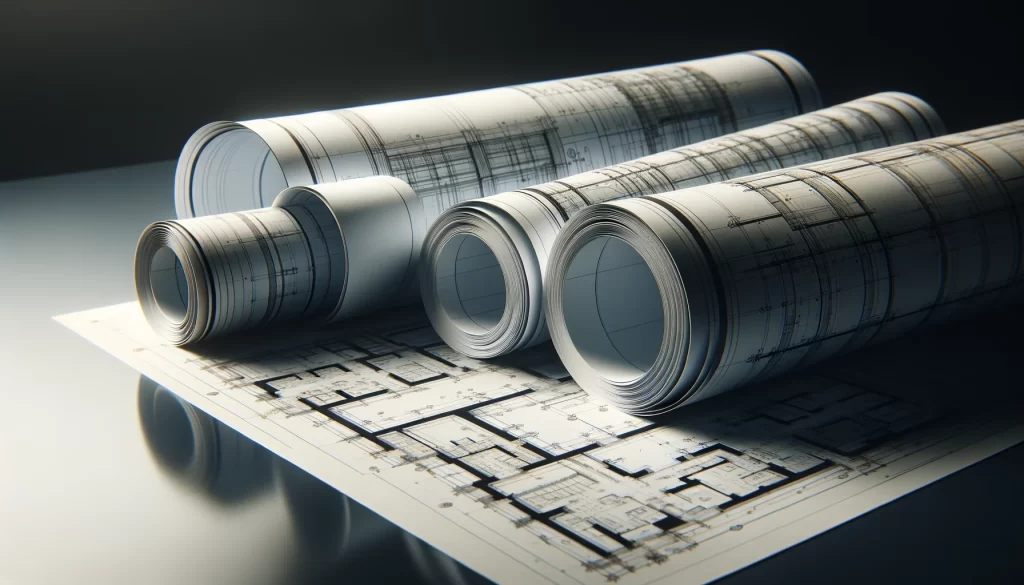
Supply Chain Collaboration and Integration
Blueprints
Supplychain360 blueprints offer an extensive collection of toolkits enabling swift access to best practice to enhance operations or to enable robust decision making.
Supply chain leaders face the critical challenge of enhancing operational efficiency while navigating complex, global networks. This blueprint addresses the urgent need for agility and sustainability by detailing how to implement cross-company lean initiatives effectively.
By streamlining operations and reducing waste, this guide not only improves responsiveness to market changes but also bolsters competitiveness and customer satisfaction. The comprehensive steps, best practices, and metrics provided here are designed to foster a culture of continuous improvement, equipping you with the tools to navigate the intricacies of modern supply chains successfully.
Detailed Implementation Steps: Executing Cross-Company Lean Strategies
Step 1: Establish a Lean Leadership Team
Action Items:
Select leaders from various departments (e.g., manufacturing, logistics, procurement) to form a core team.
Ensure the team is trained in lean principles and methodologies, such as Six Sigma or Kaizen.
Criteria for Team Selection:
Experience in project management and process improvement.
Ability to influence cross-departmental collaboration.
Step 2: Conduct a Comprehensive Process Audit
Action Items:
Utilize tools like Value Stream Mapping to identify current state processes across the company.
Document inefficiencies, waste (both material and time), and areas for improvement.
Models/Frameworks to Consider:
Lean Six Sigma’s DMAIC (Define, Measure, Analyze, Improve, Control) model to structure the audit and subsequent analyses.
Step 3: Define Lean Objectives and Targets
Action Items:
Based on the audit results, set specific, measurable, achievable, relevant, and time-bound (SMART) objectives.
Align these objectives with overall business goals and cross-company capabilities.
Criteria for Objective Setting:
Potential impact on operational efficiency and cost reduction.
Feasibility and relevance to overall strategic direction.
Step 4: Design Lean Process Solutions
Action Items:
Develop new process flows that eliminate waste and reduce steps necessary to complete a task.
Employ technology like ERP systems to support new processes.
Models/Frameworks to Consider:
Use the PDCA (Plan-Do-Check-Act) cycle to pilot and refine processes before full-scale implementation.
Step 5: Implement Lean Training Programs
Action Items:
Design comprehensive training sessions for all levels of employees, focusing on lean principles and new processes.
Use interactive workshops and simulations to demonstrate the benefits and practical applications of lean methodologies.
Criteria for Training Effectiveness:
Employee engagement levels during and post-training.
Improvement in process handling and reduction in errors post-training.
Step 6: Roll Out Lean Processes
Action Items:
Begin with pilot projects in critical areas identified during the audit.
Scale successful processes across departments and partner networks.
Models/Frameworks to Consider:
Kotter’s 8-Step Change Model to manage the change process and ensure smooth adoption.
Step 7: Establish Continuous Monitoring and Feedback Loops
Action Items:
Set up real-time monitoring systems to track the performance of new lean processes.
Regularly review performance data and gather feedback from all stakeholders.
Criteria for Monitoring Success:
Achievement of initial lean objectives.
Reduction in process variability and enhancement in quality metrics.
Step 8: Foster a Culture of Continuous Improvement
Action Items:
Encourage employees to suggest improvements based on their day-to-day experiences.
Regularly update training programs and process designs based on feedback and new lean insights.
Models/Frameworks to Consider:
The Shingo Model to reinforce principles of operational excellence and cultural reinforcement.
Step 9: Scale and Sustain Lean Initiatives
Action Items:
Standardize successful processes and implement them across the multinational network.
Leverage partnerships and collaborations to extend lean practices to suppliers and customers.
Criteria for Scaling Success:
Consistency in implementation and outcomes across different regions and departments.
Positive feedback from external partners and improved supply chain integration.
Best Practices for Implementing Lean Initiatives in Supply Chain Operations
Foster Leadership Commitment:
Actionable Insight: Secure ongoing commitment from top management to drive lean initiatives. Leadership should actively participate in lean activities and reviews to underscore their importance.
Enhance Visibility Across the Supply Chain:
Actionable Insight: Implement systems that provide real-time data and transparency across all stages of the supply chain. This could involve integrating advanced tracking systems and IoT devices to monitor inventory levels, delivery status, and production schedules.
Strengthen Supplier Relationships:
Actionable Insight: Develop strategic partnerships with suppliers to ensure they are aligned with your lean objectives. Regular collaboration and shared lean training sessions can help synchronize efforts and improve overall efficiency.
Invest in Technology and Automation:
Actionable Insight: Leverage technology to automate routine tasks and gather actionable insights through data analytics. For instance, using AI to predict demand patterns or robotics to optimize warehouse operations can significantly reduce waste and enhance responsiveness.
Continuous Employee Engagement and Training:
Actionable Insight: Maintain a program of continuous education and involvement for employees at all levels. Regular lean training, workshops, and feedback sessions encourage a culture of continuous improvement and help identify new areas for lean application.
Standardize Processes and Document Best Practices:
Actionable Insight: Create standard operating procedures for tasks across the supply chain. Documentation of processes and regular updating of procedural manuals are crucial for maintaining consistency and quality, especially in a large, multinational environment.
Implement Regular Audits and Adjustments:
Actionable Insight: Conduct periodic audits of lean practices to ensure they are being followed and to gauge their effectiveness. Use audit results to make informed adjustments to processes, addressing any new challenges or inefficiencies that arise.
By integrating these best practices with the steps outlined in the blueprint, supply chain leaders can enhance the likelihood of successful lean implementation and create a more resilient, efficient supply chain network.
Key Metrics and KPIs for Lean Supply Chain Initiatives
Lead Time Reduction:
Measurement: Track the time from order placement to delivery completion.
Interpretation: A decrease in lead time indicates improved process efficiency and faster response to customer demands.
Inventory Turnover Rate:
Measurement: Calculate how often inventory is sold and replaced over a specific period.
Interpretation: Higher turnover rates suggest better inventory management and reduced holding costs.
On-Time Delivery (OTD):
Measurement: Measure the percentage of shipments delivered on or before the promised delivery date.
Interpretation: High OTD rates reflect customer satisfaction and reliability of the supply chain processes.
Defects Per Million Opportunities (DPMO):
Measurement: Track the number of defects in the production process per million opportunities.
Interpretation: Lower DPMO indicates higher product quality and fewer production errors.
Customer Satisfaction Score (CSS):
Measurement: Use surveys and feedback tools to rate customer satisfaction.
Interpretation: Higher scores are indicative of effective lean practices impacting the end-user positively.
Cost Reduction:
Measurement: Monitor overall cost savings achieved through lean initiatives.
Interpretation: Continued cost reduction is a sign of effective waste elimination and operational efficiency.
These KPIs provide a comprehensive view of the health and efficiency of supply chain operations. By regularly tracking and analyzing these metrics, supply chain directors can make informed decisions, continue to optimize processes, and ultimately enhance the overall performance and competitiveness of their operations.
Implementation Challenges and Solutions for Lean Supply Chain Initiatives
Cultural Resistance to Change:
Challenge: Employees at various levels may resist adopting new methodologies, particularly in diverse cultural settings where traditional practices are deeply ingrained.
Solution: Foster a culture of inclusion and participation by involving employees in the planning stages. Use training and communication strategies to demonstrate the personal and collective benefits of lean initiatives.
Alignment Across Multiple Facilities:
Challenge: Ensuring consistent implementation of lean processes across geographically dispersed facilities can be difficult, leading to variability in performance.
Solution: Standardize processes through detailed documentation and regular training sessions. Employ centralized monitoring tools to track compliance and performance consistently across all locations.
Integration of IT Systems:
Challenge: Merging existing IT systems with new digital tools necessary for lean operations can be technically challenging and costly.
Solution: Conduct a thorough IT audit to understand existing capabilities and limitations. Develop a phased integration plan that allows gradual adaptation to new systems, supplemented with robust training in IT skills for relevant staff.
Supply Chain Complexity:
Challenge: Complex supply chains with numerous stakeholders can complicate the implementation of streamlined processes.
Solution: Implement a tiered approach to integration, starting with core suppliers and gradually extending to broader network participants. Utilize collaboration platforms for better coordination and transparency.
Maintaining Customer Service Levels:
Challenge: Adjusting processes might temporarily disrupt service levels, affecting customer satisfaction.
Solution: Engage with customers throughout the transition, keeping them informed of changes and expected benefits. Implement contingency plans to handle disruptions effectively without impacting service quality.
Measuring Impact and Sustaining Improvement:
Challenge: It can be difficult to track the real impact of lean initiatives and sustain improvements over time.
Solution: Develop a set of clear, relevant KPIs to measure the short-term and long-term impact of lean practices. Regularly review these metrics and adjust strategies as necessary to maintain momentum and continuous improvement.
By anticipating these challenges and preparing solutions, supply chain leaders can ensure a smoother transition to lean practices and achieve sustainable benefits. This proactive approach helps minimize disruptions and maximizes the effectiveness of lean supply chain initiatives.
This blueprint empowers supply chain leaders to dramatically enhance efficiency and responsiveness across global networks. By applying these lean initiatives, you’ll achieve sustained operational excellence, reduce costs, and improve customer satisfaction, ensuring your organization stays competitive in a dynamic marketplace.
Unlock full access to an array of blueprints and essential resources by subscribing to SupplyChain360. Stay ahead of industry trends and elevate your supply chain strategies—subscribe now to transform knowledge into action and drive success in your operations.