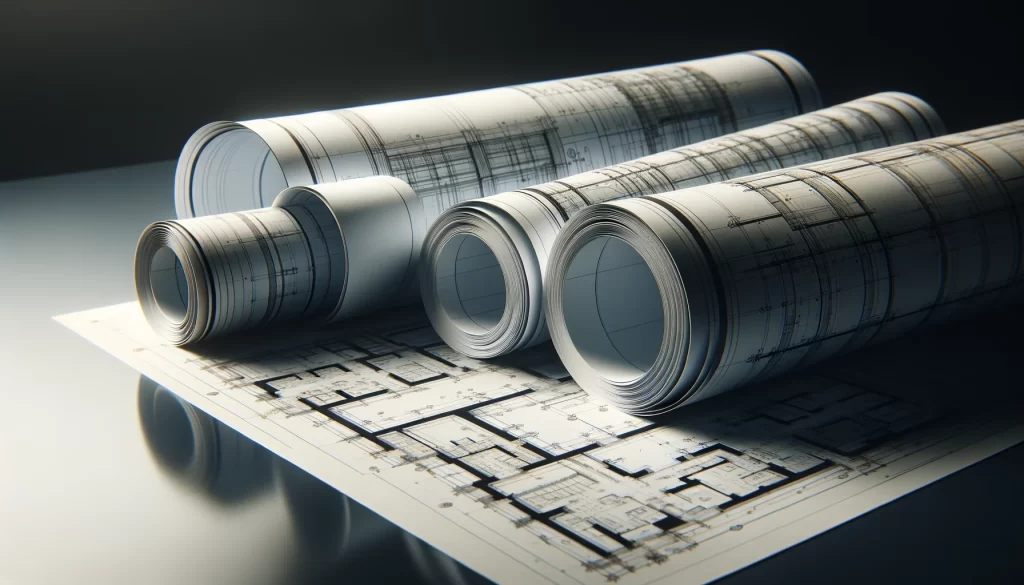
TECHNOLOGY
Blueprints
This blueprint outlines a step-by-step approach for implementing real-time transportation visibility platforms, focusing on integration strategies, best practices, and key performance metrics to optimize supply chain operations.
Real-time transportation visibility platforms are crucial for modern supply chains facing the dual challenge of maintaining efficiency and managing disruptions effectively. This blueprint provides a structured approach to implementing these platforms, emphasizing the integration of real-time data to optimize logistics operations.
Supply chain leaders will find this guide invaluable for enhancing operational transparency and responsiveness. By detailing specific implementation steps, best practices, and metrics for success, the blueprint equips your team with the necessary tools to ensure a smooth transition and tangible improvements.
Moreover, adopting the strategies outlined here will not only streamline processes but also improve decision-making capabilities, directly impacting profitability and customer satisfaction. Through practical solutions to common challenges, this blueprint is designed to bolster your supply chain’s resilience in a dynamic global market.
Implementation Steps for Real-Time Transportation Visibility Platforms
Step 1: Assessment and Planning
1.1 Conduct a Supply Chain Diagnostic: Utilize tools like the SCOR (Supply Chain Operations Reference) model to assess current supply chain performance and pinpoint inefficiencies where real-time visibility could bring improvements.
1.2 Define Specific Business Needs: Conduct workshops with stakeholders to define critical areas needing transparency, such as in-transit visibility, inventory levels, or shipment statuses.
1.3 Technology Gap Analysis: Compare current technological capabilities with industry benchmarks to identify gaps. Use frameworks like Gartner’s IT Score for Supply Chain to evaluate maturity levels and technology needs.
1.4 Risk Assessment: Perform a risk assessment focusing on potential disruptions and integration challenges. Utilize FMEA (Failure Modes and Effects Analysis) to systematically explore potential failures within logistics operations.
1.5 Set Implementation Goals: Based on the diagnostic and gap analysis, set clear, quantifiable goals such as reducing lead times by 15% or increasing delivery accuracy by 20%.
Step 2: Technology Selection
2.1 Establish Technology Criteria: Develop a matrix of essential features and advanced functionalities needed, such as GPS tracking capabilities, user interface ease, API integrations, and data analytics features.
2.2 Vendor Shortlisting: Utilize industry reports and analyst rankings, like those from Gartner or Forrester, to shortlist vendors that match the established criteria.
2.3 Request for Proposal (RFP) Process: Draft and distribute an RFP to shortlisted vendors, detailing requirements and asking for detailed proposals and product demonstrations.
2.4 Vendor Evaluation and Selection: Employ a weighted scoring system to evaluate vendor responses based on technology alignment, cost-effectiveness, support services, and client references.
2.5 Contract Negotiation and Finalization: Negotiate terms that ensure flexibility, scalability, and support. Include clauses for regular updates and compliance with industry standards.
Step 3: Integration and Testing
3.1 Develop an Integration Roadmap: Create a detailed project plan including timelines, milestones, and resource allocations, guided by methodologies such as Agile for iterative testing and implementation.
3.2 Technical Integration: Work with the vendor and IT team to integrate the platform with existing ERP, CRM, and SCM systems. Ensure data consistency and seamless workflow between systems.
3.3 Pilot Testing: Conduct a pilot test in a controlled environment to validate the platform’s functionality. Use specific case scenarios to test system robustness and end-user usability.
3.4 System Validation: Engage in comprehensive testing, including stress tests and performance assessments, to ensure the platform meets all technical and business requirements.
3.5 Go-Live Support: Establish a support framework with the vendor to address any issues during the go-live phase, ensuring 24/7 technical support and rapid issue resolution.
Step 4: Training and Roll-out
4.1 Training Program Development: Develop a detailed training program that includes both e-learning and in-person workshops tailored to different user groups’ needs.
4.2 Training Delivery: Conduct training sessions, leveraging experts from the vendor side and in-house champions who can guide and support other users.
4.3 Phased Roll-out Strategy: Implement the platform in phases, starting with less complex logistics routes or departments and gradually expanding to cover all areas.
4.4 Feedback Loop Establishment: Set up mechanisms to collect user feedback regularly, which will inform necessary adjustments and additional training needs.
Step 5: Ongoing Management and Optimization
5.1 Performance Monitoring: Use dashboards and real-time analytics to monitor the system’s performance and the impact on logistics operations continuously.
5.2 Continuous Improvement Program: Establish a continuous improvement program that utilizes Six Sigma or Kaizen principles to make incremental enhancements to the logistics processes.
5.3 Regular System Reviews and Updates: Schedule regular review meetings with the vendor to discuss updates, upgrades, and innovations that could benefit the company.
5.4 Advanced Analytics and AI Adoption: Explore opportunities to integrate advanced analytics, machine learning, and AI to further enhance predictive capabilities and decision-making processes.
Best Practices for Implementing Real-Time Transportation Visibility
Prioritize Data Quality: Begin with ensuring that data inputs are accurate and timely. High-quality data is fundamental for real-time systems to provide reliable insights and actionable intelligence. Establish strict data governance policies to maintain the integrity and accuracy of the data collected from various sources.
Engage Stakeholders Early: Involvement of all key stakeholders from the initial phases is crucial. This includes not only internal teams like IT, operations, and customer service but also external partners like carriers and logistics service providers. Early engagement helps in aligning the goals of the project with the expectations and capabilities of all parties involved.
Ensure Scalability and Flexibility: Choose solutions that can scale and adapt as business needs evolve. The selected platform should be able to integrate new technologies and accommodate increasing amounts of data without performance degradation. Flexibility in adapting to new business models or changes in supply chain configuration is essential.
Leverage Advanced Analytics: To maximize the benefits of implementing transportation visibility platforms, integrate advanced analytics capabilities. Use predictive analytics to anticipate delays or issues based on real-time data and historical trends. This enables proactive management of potential disruptions and enhances decision-making processes.
Implement Robust Training Programs: Comprehensive training programs are vital for ensuring that all users are proficient in using the new system. Tailored training that addresses the specific needs of different user groups within the organization can foster better adoption and utilization of the platform.
Focus on Continuous Improvement: Post-implementation, continually monitor the system’s performance and gather feedback from users. Use this information to refine and optimize the platform. Establish a culture of continuous improvement by regularly reviewing system capabilities and performance against industry benchmarks.
Develop a Contingency Plan: Even with real-time data, disruptions are inevitable. Develop robust contingency plans that can be activated in response to data insights. This ensures that the organization remains resilient and responsive in the face of unexpected supply chain challenges.
Key Metrics and KPIs for Measuring Success in Real-Time Transportation Visibility
Implementing real-time transportation visibility platforms transforms supply chain management by providing enhanced transparency and responsiveness. To measure the effectiveness of these platforms, supply chain directors should focus on a set of critical Key Performance Indicators (KPIs):
On-Time Delivery Rate
Track the percentage of orders delivered on the promised date. This KPI is crucial for assessing the reliability of the logistics operations enhanced by real-time visibility. Higher rates indicate more efficient and predictable delivery schedules.
Shipment Tracking Accuracy
Measure the accuracy of real-time updates provided by the visibility platform. This metric assesses how closely the reported locations and statuses of shipments match the actual conditions. High accuracy ensures that decision-making is based on reliable data.
Inventory Levels
Monitor changes in inventory levels to manage stock more effectively. Real-time visibility allows for tighter inventory control, reducing both overstock and stockouts, and optimizing storage costs.
Freight Cost per Unit
Calculate the transportation cost per unit shipped. This KPI helps in understanding cost efficiency improvements resulting from more effective routing, load optimization, and carrier performance management enabled by the visibility platform.
Customer Satisfaction Score
Evaluate customer feedback regarding the timeliness and reliability of deliveries. This qualitative metric can be quantified through regular surveys and directly correlates to the transparency provided by real-time tracking.
Response Time to Disruptions
Measure the average time it takes to respond to and resolve unexpected disruptions in the supply chain. Faster response times, facilitated by real-time alerts from the visibility platform, can significantly mitigate potential impacts on service and costs.
Tracking these KPIs requires a robust analytics dashboard that aggregates data from the transportation visibility platform in real-time. Supply chain directors should regularly review these metrics, comparing them against historical performance and industry benchmarks, to continually refine and optimize their logistics operations.
Implementation Challenges and Solutions for Real-Time Transportation Visibility Platforms
Implementing real-time transportation visibility platforms involves various challenges that can impact the effectiveness and efficiency of supply chain operations. Here are some common obstacles along with practical solutions to help supply chain leaders successfully navigate these issues:
Integration Complexity
Solution: Employ a middleware solution that can act as an intermediary, ensuring smooth data flow between the new platform and existing ERP or SCM systems. Consider modular platforms that can be integrated piecemeal to reduce disruption.
Data Quality and Consistency
Solution: Implement stringent data validation rules and regular audits to maintain data integrity. Utilize automated tools to cleanse and verify data before it enters the system.
User Adoption and Resistance to Change
Solution: Conduct comprehensive training sessions that emphasize the benefits and improved ease of operations provided by the platform. Establish a change management team to support employees through the transition.
Scalability Concerns
Solution: Choose a platform designed with scalability in mind, one that offers cloud-based services and flexible architecture to accommodate growth without requiring significant restructuring.
Privacy and Security Risks
Solution: Implement advanced cybersecurity measures, such as encryption and multi-factor authentication. Regularly update security protocols and conduct penetration testing to identify and address vulnerabilities.
Cost Management
Solution: Conduct a thorough cost-benefit analysis before implementation to ensure the long-term gains justify the expenditure. Explore phased implementation strategies to spread out costs over time.
Regulatory Compliance
Solution: Stay informed about relevant regulations and ensure the platform includes features that facilitate compliance. Engage legal experts to regularly review compliance status and adjust operations as necessary.
By anticipating these challenges and planning solutions ahead of time, supply chain leaders can enhance the likelihood of successful implementation of transportation visibility platforms. This proactive approach not only addresses the challenges but also optimizes supply chain operations, aligning with the keyphrase “implementing transportation visibility platforms.”
This blueprint provides a strategic roadmap for implementing transportation visibility platforms, enabling supply chain leaders to enhance efficiency and responsiveness. By adopting the outlined steps and best practices, your organization can expect improved operational transparency, reduced costs, and elevated customer satisfaction, ensuring a competitive edge in the rapidly evolving logistics landscape.
Unlock full access to a wealth of expertise with a subscription to SupplyChain360. Stay ahead of industry trends and enhance your supply chain strategies by subscribing today. Gain exclusive access to comprehensive blueprints and essential resources designed to drive your business forward.