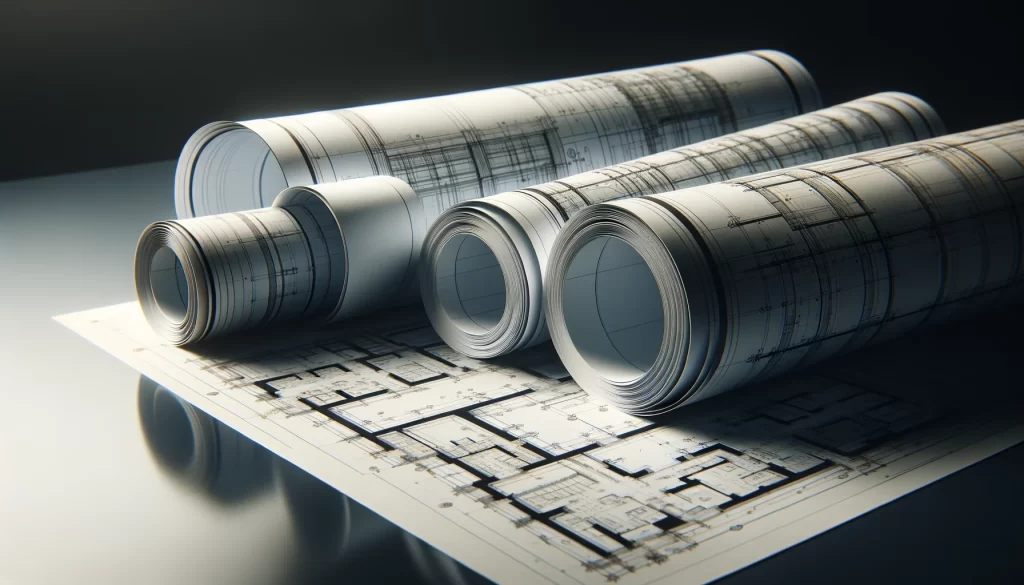
Supply Chain Collaboration and Integration
Blueprints
Supplychain360 blueprints offer an extensive collection of toolkits enabling swift access to best practice to enhance operations or to enable robust decision making.
Developing robust crisis management protocols is essential for maintaining operational continuity. This blueprint provides supply chain leaders with a structured approach to anticipate, mitigate, and manage crises effectively.
This blueprint provides actionable steps, modern frameworks, and best practices designed to fortify supply chain resilience. By following this guide, supply chain leaders can enhance their preparedness, reduce downtime, and protect their organizations from the financial and reputational impacts of crises.
Utilizing this blueprint ensures a comprehensive, proactive approach to crisis management, delivering significant benefits and safeguarding your supply chain operations.
Implementation Steps for Developing Joint Protocols for Crisis Management
Step 1: Risk Assessment and Crisis Identification
Define the Scope of Risk: Collaborate with stakeholders from various sectors of the business to comprehensively identify all potential crises that could impact different elements of the supply chain. Focus should be on environmental, technological, economic, and political risks.
Utilize Risk Assessment Models: Implement advanced risk assessment models like ISO 31000 or the COSO Enterprise Risk Management Framework to systematically evaluate and categorize risks. These models provide a structured approach to risk management by focusing on risk identification, analysis, and monitoring.
Prioritize Risks: Employ a risk matrix to classify risks based on their likelihood and potential impact. This helps in focusing resources and planning for the most significant threats first. Utilize tools like the Risk Impact/Probability Chart to visualize and prioritize risks effectively.
Step 2: Developing a Unified Crisis Response Framework
Establish Crisis Management Team: Formulate a dedicated crisis management team comprising senior members from key functions such as logistics, legal, HR, and IT across different geographies. This team should have clear authority and predefined roles during a crisis.
Define Roles and Responsibilities: Develop a detailed plan that outlines specific roles, responsibilities, and the chain of command during a crisis to avoid confusion and delays in decision-making.
Adopt Best Practice Frameworks: Integrate established frameworks such as the Incident Command System (ICS) or the Business Continuity Institute’s Good Practice Guidelines. These frameworks provide a proven structure for planning, responding, and recovering from disruptive incidents.
Step 3: Protocol Standardization Across Borders and Businesses
Create a Common Language: Develop a standardized set of terms and procedures that are universally understood within the multinational company to prevent miscommunication in high-stress environments.
Legal and Compliance Checks: Regularly update the protocols to ensure compliance with the latest international, national, and local regulations. Consider legal variations across jurisdictions that may affect protocol deployment.
Documentation: Produce clear, comprehensive documentation of all protocols. This documentation should be regularly reviewed and kept accessible in digital and physical formats for easy reference during a crisis.
Step 4: Implementation of Communication Channels and Information Sharing Systems
Establish Communication Tools: Implement state-of-the-art communication tools that can operate under various conditions, including systems that are resilient to power outages and server failures.
Secure Information Sharing Platforms: Deploy secure, integrated platforms like ERP systems coupled with cloud-based solutions to facilitate real-time information sharing. Ensure these systems are protected against cyber threats with up-to-date security measures.
Feedback Mechanisms: Designate feedback channels to gather insights from operational fronts during a crisis. Use tools like real-time dashboards to monitor feedback and adjust strategies dynamically.
Step 5: Training and Simulations
Develop Training Programs: Craft detailed training programs tailored to different roles within the crisis management framework, emphasizing practical skills, communication, and problem-solving in crisis conditions.
Conduct Simulations: Execute full-scale simulations involving all levels of the organization to test the robustness of crisis protocols. Simulations should include a variety of crisis scenarios, from natural disasters to cyber-attacks.
Review and Adapt: Analyze the outcomes of simulations to identify gaps in both the crisis response strategies and individual performances. Adjust training and protocols based on these insights to fortify the overall crisis management plan.
Step 6: Review and Continuous Improvement
Scheduled Reviews: Set up semi-annual or annual reviews to evaluate the effectiveness and relevance of the crisis management protocols. These reviews should involve updates based on recent crises or near misses.
Leverage Technology: Utilize cutting-edge technology like predictive analytics and machine learning to enhance the ability to monitor and predict potential disruptions, thus proactively adjusting protocols.
Stakeholder Feedback: Establish ongoing communication with all stakeholders, including suppliers, customers, and community leaders, to obtain external perspectives on the crisis management process. Use structured surveys and focus groups to collect and analyze feedback.
Best Practices for Implementing Crisis Management Protocols in Supply Chain Operations
Integrate Crisis Management into Corporate Culture: Cultivate a culture of preparedness by embedding crisis management into the core values of the organization. Regularly communicate the importance of readiness and resilience to all employees to foster a proactive mindset.
Regular Training and Awareness Programs: Develop ongoing training sessions that are tailored to various roles within the organization. Focus on practical exercises and real-world scenarios that could affect the supply chain. Encourage active participation and provide updates on procedures and technology tools regularly.
Diversify Supply Sources: Mitigate risks associated with supply chain disruptions by diversifying supplier networks. Establish relationships with multiple suppliers in different geographic locations to ensure continuity of supply during regional crises.
Leverage Technology for Enhanced Visibility: Implement advanced technologies such as IoT (Internet of Things), AI (Artificial Intelligence), and blockchain to gain real-time visibility into supply chain operations. These technologies can help predict potential disruptions and automate responses for faster recovery.
Establish Strong Communication Networks: Build robust communication channels that can withstand crisis conditions. Ensure that all stakeholders, including suppliers, customers, and internal teams, have access to a common platform where updates are shared efficiently and transparently.
Continuous Improvement through Feedback Loops: Set up mechanisms to capture lessons learned from past crises and from regular training simulations. Use this feedback to continuously improve crisis management protocols and training methods.
Develop a Comprehensive Recovery Plan: Create a detailed recovery plan that outlines specific steps to restore operations to normal levels post-crisis. The plan should include timelines, responsible parties, and resources needed for effective implementation.
By following these best practices, supply chain leaders can ensure their operations are better prepared to handle unexpected disruptions. These strategies not only help in managing crises when they occur but also strengthen the overall resilience of the supply chain against future challenges.
Key Metrics and KPIs for Measuring Success in Crisis Management
Time to Crisis Recognition and Response Initiation: Measure the time taken to identify a crisis and initiate the response. A shorter recognition and response time indicates a more effective and efficient crisis management protocol. Track this metric using timestamps from incident detection to the first response action logged in the crisis management system.
Communication Effectiveness: Assess the clarity, frequency, and timeliness of communications during a crisis. This can be measured by surveying stakeholders on their satisfaction with communication, tracking the number of communication breakdowns, and monitoring the response times to information requests.
Supply Chain Disruption Duration: Track the length of time that supply chain operations are impacted by a crisis. Shorter disruption durations indicate more effective crisis management. Use historical data and incident logs to monitor this metric.
Recovery Time Objective (RTO): Measure the time taken to restore operations to normal levels after a crisis. This KPI helps in evaluating the efficiency of the recovery plan. Compare actual recovery times against predefined recovery targets to gauge performance.
Cost of Crisis Management: Calculate the total costs incurred during a crisis, including direct costs (e.g., emergency supplies, overtime pay) and indirect costs (e.g., lost revenue, reputational damage). This helps in assessing the financial impact and the cost-effectiveness of the crisis management efforts.
Stakeholder Satisfaction: Evaluate the satisfaction levels of stakeholders, including suppliers, customers, and employees, post-crisis. This can be done through surveys and feedback forms to measure the perceived effectiveness of the crisis management response.
Implementation Challenges and Solutions in Crisis Management Protocols
Lack of Preparedness and Awareness: Many organizations underestimate the importance of crisis management until a disruption occurs. This leads to inadequate preparedness and a lack of awareness among employees about their roles during a crisis.
Solution: Conduct regular training sessions and simulations to keep all employees informed about crisis protocols. Integrate crisis management training into onboarding processes and hold periodic refresher courses to maintain high levels of awareness and preparedness.
Poor Communication: Ineffective communication can lead to misinformation, confusion, and delayed responses during a crisis. Communication breakdowns between different levels of the supply chain can exacerbate the situation.
Solution: Establish clear communication protocols and ensure that all stakeholders have access to reliable communication tools. Utilize technologies such as centralized communication platforms and emergency notification systems to streamline information flow.
Limited Technological Integration: Some organizations may lack the technological infrastructure required to implement advanced crisis management solutions, resulting in delayed responses and inefficient recovery efforts.
Solution: Invest in modern technologies such as IoT, AI, and blockchain to enhance visibility and automate response actions. Prioritize the integration of these technologies into existing supply chain management systems to ensure seamless operation during a crisis.
Resistance to Change: Implementing new crisis management protocols can face resistance from employees and stakeholders who are accustomed to existing processes. This resistance can hinder the adoption of new practices.
Solution: Involve key stakeholders in the development of crisis management protocols to gain their buy-in. Communicate the benefits of the new protocols clearly and provide support during the transition phase. Encourage feedback and make adjustments as needed to ease the implementation process.
Resource Constraints: Limited resources, including time, budget, and personnel, can pose significant challenges to the implementation of comprehensive crisis management protocols.
Solution: Prioritize crisis management in budget allocations and seek external funding or partnerships if necessary. Streamline processes to make efficient use of available resources and consider phased implementation to manage resource constraints effectively.
Supply Chain Complexity: The complexity of modern supply chains, with multiple interconnected nodes and global operations, makes it challenging to implement uniform crisis management protocols.
Solution: Develop flexible and scalable protocols that can be adapted to different parts of the supply chain. Use technology to map out supply chain networks and identify critical nodes that require focused crisis management efforts.
By anticipating these challenges and implementing the proposed solutions, supply chain leaders can enhance the resilience and effectiveness of their crisis management protocols. This proactive approach will help in mitigating the impact of crises and ensuring continuity of operations.
By implementing this blueprint, supply chain leaders can enhance crisis preparedness, minimize disruptions, and protect their organization’s reputation and finances. Embrace these strategies to ensure resilient and efficient supply chain operations.
Subscribe to SupplyChain360 today for exclusive access to more comprehensive blueprints and valuable resources designed to optimize your supply chain management. Stay ahead of industry challenges and drive success with expert insights and practical tools.