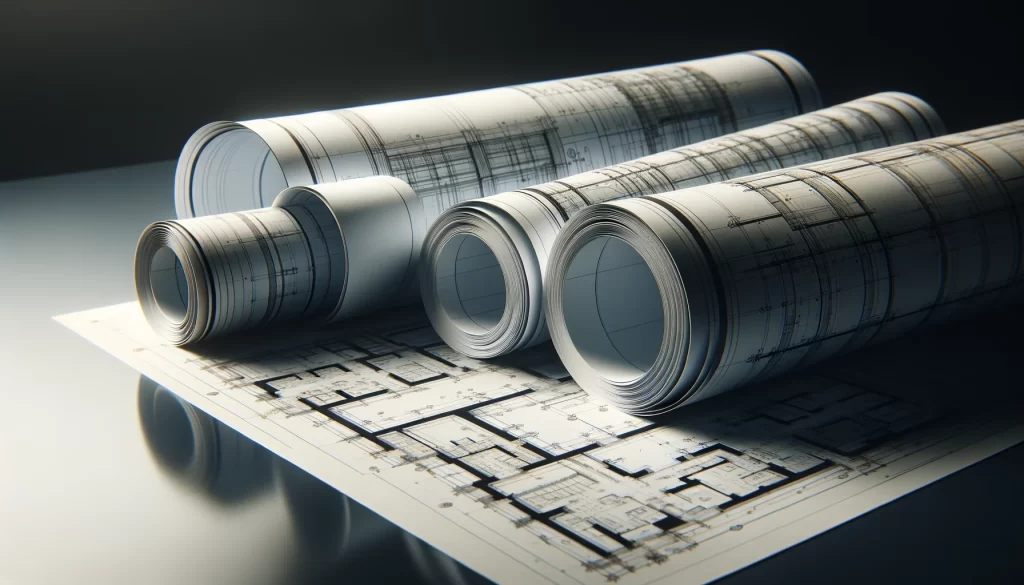
forecasting
Blueprints
This blueprint provides a detailed guide for centralizing forecasting tools within multinational supply chains, offering strategies, best practices, key metrics, and solutions to common implementation challenges.
Accurate demand forecasting play a critical role in operational efficiency and market responsiveness. This blueprint, focusing on the centralization of forecasting tools, addresses the complex challenge of disparate data and inconsistent forecasting processes across multinational corporate structures.
Centralization not only streamlines communication and decision-making but also enhances the accuracy of demand predictions and the efficiency of inventory management. By integrating advanced forecasting tools and establishing unified data practices, companies can achieve significant cost savings, reduced waste, and improved service levels.
This guide provides a systematic approach to implementing centralized forecasting tools, detailed implementation strategies, best practices, essential metrics for measuring success, and solutions to common challenges. Adopting this blueprint will equip supply chain directors with the necessary tools to optimize their forecasting capabilities, thereby strengthening their supply chain resilience and competitive advantage.
Detailed Implementation Guide for Centralizing Forecasting Tools
Step 1: Comprehensive Assessment of Forecasting Capabilities
– Audit Existing Systems: Conduct an in-depth analysis of current forecasting tools, methodologies, and data sources. Evaluate software performance, ease of use, and suitability for scaling within a global operational framework. Assess the accuracy of existing forecasts using historical data comparisons and identify patterns of forecast errors.
– Stakeholder Engagement: Organize structured interviews with stakeholders across various departments (sales, marketing, operations, finance) to understand their specific forecasting needs and pain points. Facilitate focus groups to unearth underlying issues that impact forecasting accuracy and operational efficiency.
– Gap Analysis: Utilize the SCOR model to benchmark current processes against industry best practices, focusing on areas such as Plan, Source, Make, Deliver, and Return. Document all findings in a detailed report highlighting key areas for improvement, potential risks, and the impact of current limitations on business operations.
– Define Project Scope and Objectives: Collaborate with senior management to set strategic objectives for the centralization initiative, such as cost reduction, inventory optimization, or service level improvements. Create a clear project scope document outlining expected outcomes, project timelines, and critical milestones.
Step 2: Selecting and Implementing a Unified Forecasting Platform
– Develop Technical Requirements: Compile a comprehensive list of technical specifications required in the new system, including real-time data processing, AI and machine learning capabilities, and multi-user environment support. Ensure compatibility with existing IT infrastructure and data compliance standards (e.g., GDPR, CCPA).
– Market Evaluation and Vendor Selection: Conduct a thorough market scan to identify software vendors that meet the technical and operational requirements. Use a detailed RFP (Request for Proposal) process to solicit vendor proposals and a scoring matrix to evaluate them based on functionality, support, integration capabilities, and cost.
– System Customization and Integration: Work closely with the selected vendor to customize the forecasting tool to fit unique business needs and integrate seamlessly with existing ERP, CRM, and other critical systems. Plan for robust data migration strategies to ensure data integrity and continuity during the transition phase.
– Vendor Collaboration and Contract Negotiation: Engage in detailed negotiations to ensure favorable terms in areas such as scalability, technical support, training, and future upgrades. Establish SLAs (Service Level Agreements) and regular performance reviews to hold vendors accountable for continuous system improvement.
Step 3: Data Integration and System Configuration
– Data Consolidation Strategy: Develop a master data management plan to standardize data definitions and formats across all sources, ensuring a unified view within the new forecasting system. Implement data governance practices to maintain data quality and accessibility.
– Integration of Data Sources: Use advanced data integration tools and middleware solutions to connect disparate data sources. Ensure the integration supports both batch and real-time data processing. Test data flows thoroughly to validate the accuracy and completeness of data integration.
– System Configuration and Optimization: Configure the forecasting models within the platform, customizing parameters and settings for different product lines and geographic markets. Optimize the system setup to leverage machine learning algorithms for predictive analytics and scenario planning.
Step 4: Training, Change Management, and Deployment
– Comprehensive Training Programs: Develop detailed training materials tailored to different user roles within the organization, from system administrators to end-users. Offer a mix of training formats, including in-person workshops, live webinars, and self-paced online modules.
– Change Management Execution: Implement a structured change management program following the Prosci ADKAR model, focusing on building awareness, desire, knowledge, ability, and reinforcement among all employees. Establish a network of change champions within the organization to facilitate smoother adoption and to provide support during the transition.
– Phased Rollout and User Adoption Monitoring: Initiate a phased rollout strategy starting with a pilot in a controlled environment or selected business unit, followed by company-wide implementation. Use KPIs to monitor system adoption and effectiveness, gathering user feedback to continuously refine the tool and training approaches.
Best Practices for Implementing Centralized Forecasting Tools in Supply Chain Operations
When embarking on the journey to centralize forecasting tools within supply chain operations, adhering to proven best practices can significantly enhance the effectiveness and success of the implementation. Here are essential practices to consider:
1. Engage All Levels of the Organization:
Comprehensive Involvement: Ensure that the initiative has support from both top management and operational levels. Active engagement from all levels promotes buy-in and facilitates smoother change management.
Continuous Communication: Maintain open lines of communication throughout the project to keep all parties informed and aligned. Regular updates and feedback loops help preempt resistance and foster a collaborative environment.
2. Emphasize Data Quality:
Data Integrity Checks: Implement rigorous data validation and cleansing processes to maintain high data quality. Accurate data is crucial for effective forecasting and decision-making.
Ongoing Data Management: Establish procedures for ongoing data management to adapt to changing data needs and ensure that the data remains reliable and relevant.
3. Leverage Technology Strategically:
Select Appropriate Tools: Choose technology solutions that not only fit the current business scale but are also scalable for future growth. Integration capabilities with existing systems are crucial to avoid silos.
Advanced Analytics: Utilize advanced analytics and machine learning to enhance predictive capabilities. These technologies can help in identifying trends and making data-driven decisions more effectively.
4. Focus on User Training and Support:
Tailored Training Programs: Develop training programs that are tailored to the specific roles and responsibilities of users. This targeted approach helps in quicker adaptation and more effective use of the new system.
Robust Support Systems: Implement a robust support system to assist users post-deployment. Ongoing support and troubleshooting are vital for addressing issues promptly and ensuring continuous system usage.
5. Monitor and Adapt:
Performance Monitoring: Regularly monitor the system’s performance using the predefined KPIs related to forecast accuracy, inventory levels, and operational efficiency.
Feedback for Continuous Improvement: Encourage feedback from users to identify areas of improvement. Regularly update the forecasting models and processes based on this feedback to adapt to new challenges and market conditions.
By following these best practices when centralizing forecasting tools, supply chain leaders can significantly improve their demand planning accuracy. This strategic approach not only optimizes operations but also ensures that the supply chain is more resilient and responsive to market dynamics. Integrating these practices alongside the blueprint will facilitate a smooth transition and maximize the benefits of centralization within multinational supply chain environments.
Key Metrics and KPIs to Measure Success in Centralized Forecasting
For supply chain directors, defining and monitoring the right key performance indicators (KPIs) is crucial to evaluating the success of centralized forecasting tools. Here’s an overview of essential metrics to track:
1. Forecast Accuracy:
Definition: Measures the precision of demand forecasts compared to actual demand. It is typically calculated as the percentage difference between forecasted and actual sales.
Tracking and Interpretation: Regularly compare forecasted data against real sales figures. Use moving averages to smooth out variability and identify trends in accuracy improvements or declines. This metric helps in refining forecasting methods and models over time.
2. Inventory Turns (Turnover):
Definition: Indicates how many times inventory is sold and replaced over a specific period, providing insight into inventory management efficiency.
Tracking and Interpretation: Calculate by dividing the cost of goods sold by the average inventory value. Higher turnover rates often suggest better inventory management, but very high turnover might lead to stockouts and missed sales, necessitating a balanced approach.
3. Order Fulfillment Cycle Time:
Definition: The time taken from receiving a customer order to delivering the product. It reflects the efficiency of the supply chain operations.
Tracking and Interpretation: Monitor the complete timeline of order processing, including picking, packing, shipping, and delivery. Reducing cycle time can improve customer satisfaction and reduce holding costs.
4. Service Level:
Definition: Measures the ability of the supply chain to meet expected delivery times and order fulfillment requests, expressed as a percentage.
Tracking and Interpretation: Track the proportion of orders meeting customer service agreements or expectations. This KPI is vital for assessing the impact of forecasting on customer satisfaction and retention.
5. Cost of Carry (Inventory Holding Cost):
Definition: The total cost associated with holding inventory, including storage, insurance, depreciation, and obsolescence.
Tracking and Interpretation: Calculate by adding all expenses related to storing unsold goods. Aim to minimize these costs without compromising the ability to meet customer demand, which can be achieved by improving forecasting accuracy.
By monitoring these KPIs, supply chain directors can obtain a clear picture of the operational impacts of their centralized forecasting efforts. These metrics not only facilitate ongoing adjustments to forecasting and inventory strategies but also support strategic decision-making to enhance overall supply chain performance.
Implementation Challenges and Solutions in Centralizing Forecasting Tools
Implementing centralized forecasting tools in multinational supply chains comes with its set of challenges. Understanding these obstacles and preparing strategies to mitigate them is crucial for a successful implementation. Here are some common challenges and practical solutions:
1. Resistance to Change
Challenge: Employees may resist new processes and tools, especially if they feel uncertain about the implications for their roles and responsibilities.
Solution: Implement comprehensive change management strategies. Begin with clear communication about the benefits and reasons behind the shift to centralized forecasting. Use the ADKAR model (Awareness, Desire, Knowledge, Ability, Reinforcement) to structure change initiatives. Provide ample training and create a feedback loop that allows employees to express concerns and receive support.
2. Data Integration Complexities
Challenge: Integrating disparate data sources can be technically challenging, particularly when dealing with different formats and legacy systems that lack compatibility.
Solution: Employ a dedicated IT integration team that specializes in data management and software integration. Use middleware solutions that can bridge different technologies and create a seamless flow of information. Regularly update data governance policies to ensure data quality and consistency.
3. High Initial Costs
Challenge: The initial investment in new software, training, and system integration can be substantial, which might deter decision-makers.
Solution: Conduct a thorough cost-benefit analysis to demonstrate the long-term savings and efficiency gains from centralized forecasting. Consider phased implementation to spread out expenses and prove ROI at each stage before further investment.
4. Scalability Concerns
Challenge: As organizations grow, their forecasting tools need to accommodate increased complexity and volume without performance degradation.
Solution: Select forecasting platforms with proven scalability. Evaluate software through pilot testing in different scenarios to ensure it can handle future growth. Regularly review system performance and upgrade capabilities as needed.
5. Maintaining Accuracy Across Global Operations
Challenge: Ensuring forecasting accuracy and consistency across various global markets can be daunting due to differing market dynamics and consumer behaviors.
Solution: Customize forecasting models to accommodate regional variations and continuously train local teams on best practices. Utilize machine learning algorithms that automatically adjust to changing patterns and trends in each market.
6. Ensuring Continuous Improvement
Challenge: After initial implementation, there might be a tendency to overlook continuous improvement of the forecasting system.
Solution: Establish a continuous improvement team tasked with regularly reviewing the forecasting processes. Set up KPIs specifically designed to measure forecasting performance and use the insights gained to refine and optimize the models.
By anticipating these challenges and preparing solutions in advance, supply chain leaders can effectively manage the transition to centralized forecasting tools, ensuring a smoother implementation and better alignment with business objectives. This proactive approach will help in optimizing supply chain operations and enhancing the accuracy of demand planning.
Adopting this blueprint for centralizing forecasting tools offers significant advantages, including enhanced demand planning accuracy, streamlined operations, and improved cost efficiencies. By implementing the outlined strategies, supply chain leaders can ensure robust scalability and responsiveness, positioning their organizations for sustained success in a dynamic global market.
Unlock the full potential of your supply chain with exclusive access to our comprehensive blueprints and expert resources. Subscribe to SupplyChain360 today and stay ahead with the latest strategies and insights tailored for top-tier supply chain management.