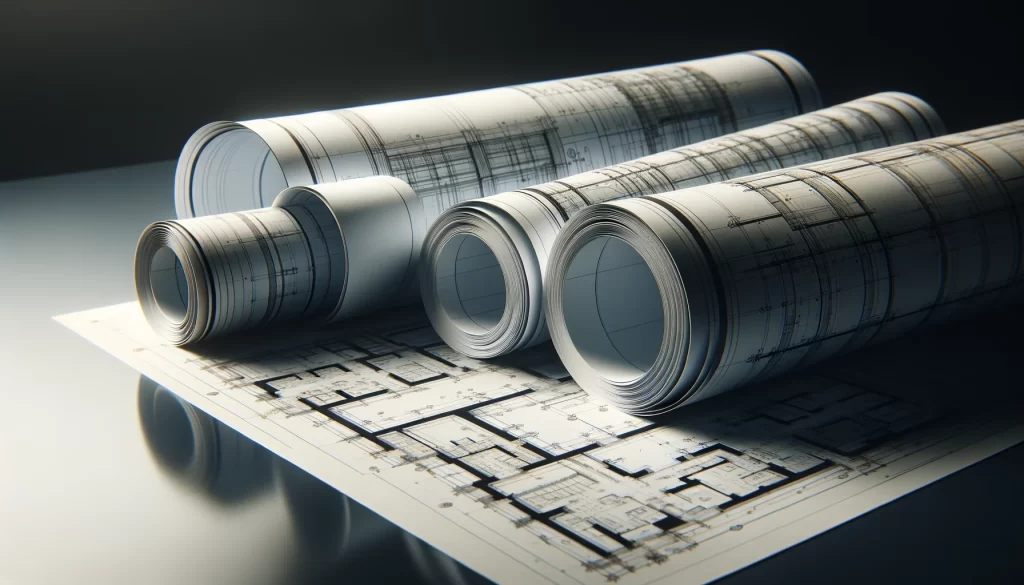
procurement
Blueprints
This blueprint provides a structured approach for supply chain leaders to effectively manage costs and optimize procurement strategies.
Strategic cost management in procurement is imperative for maintaining competitiveness in the global marketplace. This blueprint delivers a focused methodology for analyzing and controlling procurement costs effectively, tailored for supply chain leaders at multinational corporations.
By outlining specific, actionable steps, this guide helps leaders implement cost-saving strategies that are both sustainable and adaptable. The incorporation of modern tools and metrics ensures that the strategies are measurable and scalable, enhancing decision-making processes across the supply chain.
The value of this blueprint lies in its ability to transform theoretical cost management into tangible practices that drive financial performance and operational efficiency, ultimately safeguarding profit margins in an ever-evolving economic landscape.
Implementation Steps for Strategic Cost Management in Procurement
Step 1: Establish a Baseline of Current Costs
1.1 Data Collection: Collect procurement data across various departments. Consolidate data into a central database using tools like Microsoft Excel or a dedicated ERP system.
1.2 Cost Analysis: Use analytical tools to categorize expenditures by supplier, category, and department. Identify key areas where costs are higher than industry benchmarks using comparative analysis.
1.3 Baseline Establishment: Develop a cost baseline that reflects the average costs for significant spending categories. Document and share the baseline with stakeholders to establish a starting point for cost management initiatives.
Step 2: Define Cost Management Objectives
2.1 Strategic Alignment: Review the company’s overall strategic goals and align cost management objectives accordingly. Identify key stakeholders and define their roles and responsibilities in achieving these objectives.
2.2 Target Setting: Define specific, measurable, achievable, relevant, and time-bound (SMART) cost reduction targets. Break down targets by department and spending category.
2.3 Stakeholder Engagement: Conduct workshops and meetings to align all stakeholders with the cost management plan. Develop communication plans to keep stakeholders informed of progress and changes.
Step 3: Implement Total Cost of Ownership (TCO) Model
3.1 Model Education: Provide training sessions on the TCO model to procurement teams. Share resources and case studies demonstrating the benefits of TCO.
3.2 TCO Application: Develop TCO calculations for high-value items or categories. Integrate TCO results into procurement decision-making processes.
3.3 Decision Making: Use TCO outcomes to evaluate and select suppliers. Adjust procurement strategies based on TCO findings to optimize cost savings.
Step 4: Develop Supplier Evaluation and Selection Criteria
4.1 Criteria Development: Collaborate with stakeholders to define comprehensive supplier evaluation criteria. Include sustainability and compliance as key evaluation parameters.
4.2 Supplier Scorecards: Design scorecards that quantify supplier performance against defined criteria. Implement a regular review cycle to update scorecard results.
4.3 Continuous Supplier Assessment: Establish mechanisms for ongoing supplier performance monitoring. Use feedback from scorecard assessments to negotiate improvements or terminate underperforming suppliers.
Step 5: Optimize Procurement Processes
5.1 Process Mapping: Map current procurement processes from requisition to payment. Identify bottlenecks and areas for process automation.
5.2 Lean Implementation: Apply lean principles to remove unnecessary steps and reduce cycle time. Train teams on lean methodologies specific to procurement.
5.3 Technology Enhancement: Evaluate and implement e-procurement solutions that integrate with existing ERP systems. Ensure systems are user-friendly and provide adequate training for users.
6.1 Partnership Development: Identify key suppliers and develop strategies for partnership engagements. Organize partnership meetings to discuss opportunities for cost savings and process improvements.
6.2 Joint Initiatives: Collaborate on technology sharing, bulk purchasing, and joint product development initiatives. Set up a framework for sharing benefits derived from joint initiatives equitably.
6.3 Long-term Engagement: Negotiate long-term contracts with suppliers that offer cost predictability and savings. Establish regular review points to ensure contracts remain beneficial and relevant.
7.1 Analytics Implementation: Introduce advanced analytics tools that can provide deeper insights into spending patterns. Train procurement teams on how to interpret analytics reports for strategic decision-making.
7.2 Routine Reporting: Develop a schedule for routine reporting and reviews to track against cost management objectives. Use dashboards and visualization tools to make data accessible and actionable.
7.3 Adjustment Framework: Create a responsive adjustment mechanism based on analytical insights to improve procurement strategies. Foster a culture of continuous improvement, encouraging feedback and suggestions from all levels of the organization.
8.1 Training Programs: Develop and deliver comprehensive training programs that cover strategic cost management, advanced negotiation skills, and the use of new procurement technologies.
8.2 Knowledge Sharing: Implement regular knowledge sharing sessions to discuss new trends, technologies, and methodologies in procurement.
8.3 Continuous Learning: Encourage continuous professional development through certifications, seminars, and workshops in relevant fields.
9.2 Strategy Refinement: Refine strategies based on performance evaluations and changing market conditions.
9.3 Scalability Assessment: Assess the scalability of successful strategies across different parts of the organization to maximize impact.
Best Practices for Implementing Strategic Cost Management in Supply Chain Operations
1. Prioritize Transparent Communication
Maintain open lines of communication with all stakeholders, including suppliers, to ensure alignment on cost management objectives.
Provide regular updates on progress and challenges to keep all parties informed and engaged, facilitating smoother implementation.
2. Leverage Technology for Enhanced Visibility
Utilize advanced analytics and real-time tracking systems to gain better visibility into supply chain operations. This visibility is crucial for identifying cost-saving opportunities and potential bottlenecks.
Ensure that technological solutions are fully integrated with existing systems for seamless data flow and analysis.
3. Develop a Culture of Continuous Improvement
Establish mechanisms for continuous feedback from internal teams and suppliers. This will help in rapidly identifying inefficiencies and developing solutions.
Commit to regular training sessions that keep teams updated on the latest strategies and technologies in cost management.
4. Implement Strategic Sourcing
Collaborate closely with suppliers to find mutual cost reduction opportunities. This might include bulk purchasing or long-term contracts that benefit both parties.
Avoid over-reliance on single suppliers by diversifying the supplier base. This reduces risk and potentially leverages competition to achieve better pricing.
5. Focus on Total Cost of Ownership (TCO)
Instead of focusing solely on upfront costs, evaluate the total cost of ownership, which includes all costs associated with the lifecycle of a product or service. This approach provides a clearer picture of long-term savings and value.
Use TCO as a primary criterion in procurement decision-making processes to ensure sustainable cost management.
6. Enhance Supplier Relationships
Develop long-term relationships with key suppliers to foster trust and cooperation, which often leads to more favorable terms and innovations that can drive down costs.
Implement performance-based incentives that encourage suppliers to innovate and reduce costs, aligning their objectives with your strategic goals.
By following these best practices, supply chain leaders can effectively implement strategic cost management in procurement, leading to significant enhancements in efficiency and cost reduction. These actionable steps provide a robust framework for optimizing supply chain operations and achieving long-term sustainability and competitiveness.
Key Metrics and KPIs for Measuring Success in Strategic Cost Management
1. Cost Savings
Definition: Reduction in spending compared to a predefined baseline.
Tracking: Use financial management software to track expenses over time and compare against set benchmarks.
Interpretation: Consistent cost reductions indicate successful implementation of cost management strategies, while variances can signal areas needing adjustment.
2. Supplier Performance Metrics
Definition: Evaluation of supplier contribution to cost management based on quality, delivery, service, and cost.
Tracking: Develop supplier scorecards that rate these key aspects regularly.
Interpretation: High scores suggest a strong supplier alignment with business goals, whereas low scores may warrant a review of supplier contracts or negotiations.
3. Compliance Rate with Procurement Policies
Definition: The percentage of procurement activities that adhere to established internal policies and contract terms.
Tracking: Monitor procurement transactions using ERP systems to ensure they comply with corporate standards and contractual agreements.
Interpretation: High compliance rates indicate effective control and governance within the procurement function, while low rates could point to potential savings leakage or policy gaps.
4. Inventory Turnover Rate
Definition: Measures how often inventory is sold and replaced over a period.
Tracking: Analyze inventory levels and sales data to calculate turnover rates.
Interpretation: Higher turnover rates often reflect better inventory management and cost control, minimizing holding costs and reducing the risk of obsolescence.
These KPIs provide a comprehensive view of the financial health and operational efficiency within the supply chain. Regular assessment and interpretation of these metrics enable supply chain directors to make informed decisions, aligning operational activities with strategic cost management goals effectively.
Navigating Implementation Challenges in Strategic Cost Management
1. Resistance to Change
Challenge: Employees and management often resist changes to established processes and systems.
Solution: Foster a culture of continuous improvement by involving employees in the planning and implementation phases. Offer training and clear communication on the benefits of the new strategies to gain buy-in.
2. Integration with Existing Systems
Challenge: New cost management tools and processes may not easily integrate with existing IT systems.
Solution: Work closely with IT departments to ensure new systems are compatible. Consider phased rollouts of technology to monitor integration issues and adjust as needed.
3. Supplier Coordination
Challenge: Coordinating with multiple suppliers, especially in different geographical locations, can complicate cost management efforts.
Solution: Establish clear communication channels and regular check-ins with suppliers. Use technology like ERP systems for real-time data sharing and coordination.
4. Data Quality and Availability
Challenge: Inaccurate or incomplete data can lead to poor strategic decisions.
Solution: Invest in data management systems that ensure accuracy and completeness. Train staff on the importance of data quality and establish protocols for regular data audits.
5. Regulatory Compliance
Challenge: Staying compliant with diverse regulatory requirements across different regions can be daunting and resource-intensive.
Solution: Implement a compliance management system and keep up-to-date with regulatory changes. Regular training sessions for the procurement team on compliance issues are also crucial.
6. Economic Fluctuations
Challenge: Economic instability can affect pricing, supply availability, and overall cost management strategies.
Solution: Develop flexible procurement strategies that allow for quick adjustments. Build strong relationships with multiple suppliers to ensure supply chain resilience.
7. Scaling Cost Management Initiatives
Challenge: Expanding successful cost management strategies across the entire organization can be difficult.
Solution: Standardize successful practices and develop a roadmap for gradual implementation across all departments. Utilize KPIs to measure success and adapt strategies as needed for different areas of the business.
By anticipating these challenges and implementing these targeted solutions, supply chain directors can enhance their strategic cost management efforts, leading to more efficient operations and improved financial performance.
This blueprint on strategic cost management in procurement equips supply chain leaders with a comprehensive strategy to enhance cost efficiencies and optimize operations. Utilizing this guide will lead to improved financial performance, streamlined processes, and increased competitive advantage in the global market, ensuring sustainable growth and profitability for multinational corporations.
Unlock the full potential of your supply chain with exclusive access to more blueprints and resources. Subscribe to SupplyChain360 today and stay ahead of industry trends, innovations, and best practices that will transform your operations and drive success.