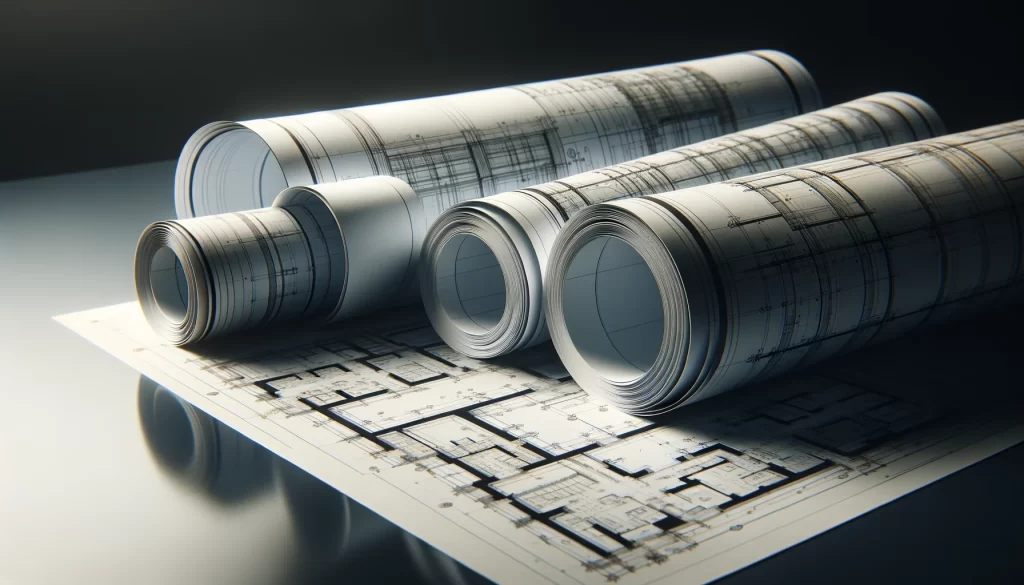
procurement
Blueprints
Supplychain360 blueprints offer an extensive collection of toolkits enabling swift access to best practice to enhance operations or to enable robust decision making.
Streamlining logistics and enhancing efficiency are crucial for business leaders tasked with reducing warehouse time and expediting delivery processes. This blueprint introduces robust cross-docking techniques designed to address these specific challenges by minimizing storage duration and maximizing throughput in real-time.
Cross-docking offers significant operational advantages by reducing dependency on warehouse storage and improving inventory turnover rates—critical factors in optimizing supply chain operations. This blueprint provides a comprehensive, actionable framework that guides supply chain leaders through implementing cross-docking strategies from the ground up. It details planning, execution, technology integration, and key performance metrics that collectively ensure a successful transformation of your logistics operations.
By adopting the strategies outlined in this blueprint, organizations will benefit from reduced operational costs, enhanced speed of delivery, and improved customer satisfaction, positioning them to thrive in competitive markets.
Detailed Implementation Guide for Cross-Docking Techniques
1. Strategic Site Selection
1.1. Geographic Considerations: Perform a logistics network analysis to identify optimal locations close to major highways, ports, and rail terminals. Traffic data and local infrastructure should be evaluated for accessibility and to minimize potential delays, along with the implications of local regulations, labor availability, and cost factors.
1.2. Facility Requirements: Space requirements should be determined based on the anticipated volume of goods and their handling needs. Facilities with adequate dock capacity and layouts that facilitate swift movement of goods between transportation modes should be prioritized, ensuring that the site supports scalability and flexibility for future expansions.
2. Efficient Layout Design
2.1. Flow Optimization: Utilize the Spaghetti Diagram principles to design the warehouse layout, minimizing unnecessary movement and streamlining the flow from receiving to shipping. Flexible docking stations should be incorporated to efficiently handle different types of goods and transport vehicles.
2.2. Technology Integration: Implement digital twins of warehouse operations to simulate and optimize flows before physical setup. Use layout-design software to create, test, and refine dock placement and goods routing paths.
3. Advanced Workforce Training
3.1. Skill Development: Develop specialized training modules focused on cross-docking operations, including handling techniques and safety protocols. Employ virtual reality (VR) simulations for training staff on complex scenarios without the risks associated with physical training.
3.2. Performance Monitoring: Establish a certification program that benchmarks employee skills against industry standards and provides ongoing assessment and feedback. Implement a mentorship system to foster skill transfer and adaptation by pairing new employees with experienced personnel.
4. Synchronized Scheduling
4.1. Integration of JIT Principles: Advanced scheduling software should be used to tightly align inbound and outbound logistics operations with production schedules and customer demand. Develop algorithms to dynamically adjust schedules based on real-time data from IoT devices and traffic updates.
4.2. Collaboration Tools: Deploy collaborative platforms that integrate internal schedules with those of suppliers and logistics partners to ensure transparency and responsiveness. Use AI-driven predictive analytics to anticipate potential delays and automatically adjust schedules.
5. Seamless Transportation Coordination
5.1. Partner Alignment: Engage with transportation partners who demonstrate capacity for electronic integration and real-time data sharing. Regularly review and optimize transportation contracts to include performance-based incentives for schedule adherence and handling specifications.
5.2. Advanced Tracking Systems: Implement GPS and RFID tracking solutions to continuously monitor goods across the supply chain. Integrate these systems with mobile apps to provide drivers and management with real-time updates and alerts.
6. Automated Handling Systems
6.1. Robotics and Automation: Deploy robotics solutions for sorting, stacking, and palletizing goods to reduce manual handling and improve speed. Automated conveyor belts tailored to the types of goods handled should be evaluated and implemented to enhance efficiency and reduce damage.
6.2. Continuous Process Evaluation: Utilize sensors and machine learning algorithms to continuously assess the performance of automated systems and identify areas for improvement. Regular updates and maintenance should be scheduled to ensure technology remains state-of-the-art and fully functional.
Best Practices for Implementing Cross-Docking in Supply Chain Operations
Implementing cross-docking techniques effectively requires adherence to several best practices that ensure efficiency and sustainability of operations. These practices not only optimize the process but also align it with broader supply chain strategies.
1. Engage in Thorough Planning and Analysis: Before initiating cross-docking, conduct a detailed analysis of the current supply chain processes to identify the most beneficial products and routes for cross-docking. Products with high turnover rates and predictable demand patterns are ideal candidates. This preliminary step ensures that cross-docking delivers maximum efficiency.
2. Foster Strong Partner Relationships: Collaboration is key in the supply chain environment. Develop strong relationships with all partners, including suppliers, transporters, and distributors. These relationships help in smoothing the flow of information and goods, which is critical for the just-in-time nature of cross-docking.
3. Implement Advanced Technology Solutions: Leverage technology to enhance visibility and control throughout the cross-docking process. Technologies such as real-time tracking systems, warehouse management systems (WMS), and transportation management systems (TMS) are essential. They provide the necessary data to make informed decisions and improve responsiveness to changing supply chain dynamics.
4. Continuous Training and Development: Regular training programs for staff on the latest cross-docking procedures and technologies are crucial. As cross-docking relies heavily on speed and efficiency, a well-trained workforce can significantly minimize handling times and errors.
5. Monitor and Optimize Continuously: Use key performance indicators (KPIs) and regular audits to measure the effectiveness of cross-docking operations. This monitoring helps in identifying areas of improvement and implementing corrective actions promptly. Continuous optimization of processes ensures that the supply chain remains agile and responsive to market changes.
6. Prioritize Scalability and Flexibility: Design cross-docking operations to be scalable and flexible. This approach allows businesses to adjust quickly to increasing volumes or changing market conditions without significant disruptions or investments.
Adopting these best practices can significantly enhance the effectiveness of cross-docking techniques, making them a powerful tool for modern supply chain leaders seeking to reduce costs and improve delivery times. This strategic approach ensures that operations remain competitive and responsive to the dynamic needs of the market.
Key Metrics and KPIs for Cross-Docking Success
To effectively measure the success of cross-docking operations within supply chain management, it’s crucial for supply chain directors to focus on a set of well-defined metrics and key performance indicators (KPIs). These metrics provide actionable insights and help gauge the efficiency, effectiveness, and overall impact of cross-docking techniques.
1. Dock-to-Dock Turnaround Time: This KPI measures the time taken for goods to move from the receiving dock to the shipping dock without entering storage. A lower turnaround time indicates higher efficiency in moving goods directly between trucks, which is the primary goal of cross-docking.
2. On-Time Shipping Rate: Tracks the percentage of shipments that leave the docking station on schedule. This metric is vital for assessing the timeliness of outbound logistics and its impact on customer satisfaction.
3. Inventory Holding Costs: Monitoring the costs associated with holding inventory is crucial in cross-docking, as the goal is to reduce these expenses by minimizing warehouse storage.
4. Order Accuracy Rate: Measures the accuracy of orders being processed through the cross-docking system. High accuracy rates signify effective handling and sorting at the dock level, reducing errors and returns.
5. Freight Carrying Costs per Unit: Analyzes the cost involved in transporting each unit of product. Efficient cross-docking should lead to a reduction in these costs by optimizing shipping methods and reducing handling steps.
To track these KPIs, supply chain directors should implement integrated IT systems such as Warehouse Management Systems (WMS) and Transportation Management Systems (TMS) that provide real-time data and analytics capabilities. Regularly reviewing these metrics allows directors to adjust operations dynamically, identify areas of improvement, and align cross-docking practices with broader supply chain objectives. Analyzing trends over time and benchmarking against industry standards can further help in interpreting the data, ensuring that the cross-docking process remains both competitive and efficient.
Navigating Challenges in Cross-Docking Implementation
Implementing cross-docking techniques within a supply chain can present various challenges that may hinder operations if not adequately addressed. Here, we identify common obstacles and propose practical, actionable solutions to help supply chain leaders successfully navigate these challenges.
1. Integration with Existing Systems
- Challenge: Integrating cross-docking operations with existing warehouse and transportation management systems can be complex, especially if the current systems are outdated or incompatible.
- Solution: Conduct a thorough system audit to identify compatibility issues and gaps. Invest in modular software solutions that can be integrated with existing systems gradually. Consider working with IT specialists who can customize interfaces and ensure seamless integration without disrupting ongoing operations.
2. Vendor Coordination
- Challenge: Effective cross-docking requires precise coordination with vendors to ensure that goods arrive just in time for immediate forwarding. Any misalignment can lead to delays and congestion at the dock.
- Solution: Strengthen communication channels with all vendors using advanced scheduling tools and collaborative platforms that provide real-time updates and adjustments. Regular alignment meetings and performance reviews can help maintain synchronization and promptly address any coordination issues.
3. Training and Labor Skills
- Challenge: Cross-docking is a fast-paced operation that demands specific skills from the workforce, such as handling specialized equipment and managing quick turnarounds. A lack of adequately trained personnel can result in operational inefficiencies.
- Solution: Develop a comprehensive training program tailored to cross-docking operations. Incorporate hands-on sessions and simulation-based training to enhance skill development. Foster a culture of continuous learning by providing regular updates and skill refreshers.
4. Space and Layout Optimization
- Challenge: Optimizing space within the docking facility to accommodate rapid loading and unloading processes can be challenging, particularly in older facilities not originally designed for cross-docking.
- Solution: Utilize lean management principles to redesign the dock layout, maximizing efficiency and minimizing unnecessary movements. If necessary, consider reconfiguring the warehouse or investing in automation technologies like conveyor belts or automated guided vehicles (AGVs) to improve flow and handling time.
5. Supply Chain Disruptions
- Challenge: Disruptions in the supply chain, such as delays from suppliers or unexpected demand spikes, can significantly impact cross-docking operations, which rely on tight scheduling and minimal inventory.
- Solution: Build robust contingency plans that include alternative suppliers and transportation options. Use predictive analytics to forecast potential disruptions and adjust operations proactively. Maintain a flexible approach to inventory management, allowing for buffer stocks when needed.
By anticipating these challenges and implementing the outlined solutions, supply chain directors can ensure the successful adoption of cross-docking techniques, leading to enhanced operational efficiency and improved supply chain performance. These insights are essential for navigating the complexities of modern supply chain environments and maximizing the benefits of cross-docking practices.
This blueprint offers a strategic pathway to implementing cross-docking techniques, enhancing supply chain efficiency and reducing operational costs. By adopting these methods, supply chain leaders can achieve faster turnaround times, improved order accuracy, and optimized logistics operations, ensuring that their systems remain agile and responsive in a competitive marketplace.
Ready to elevate your supply chain strategy? Subscribe to SupplyChain360 today and gain exclusive access to expert blueprints, in-depth resources, and the latest industry insights designed to streamline your operations and boost your competitive edge. Join us and transform your supply chain management approach!